
Disclaimer: Doing anything to your brakes can be dangerous if it is not done correctly. If you are not 100% confident in doing this, don't do it. I will not be held responsible for brakes failing.
Note: I forgot to take photos of some parts of the process, but I recycled some from the front caliper rebuild as the process is the same. So If the parts look a bit different in some of the pics, that's why.
First thing you will have to do is remove the caliper from the car or use a second set. Follow the beginning of this guide to remove the calipers from your car.
One thing that isn't mentioned in the guide above is to remove the brake line from the caliper.
What you'll need
Rebuild Kit (MB857874) You will need two of these, one for each caliper
Socket set
Rear piston removal tool (optional)
Needle nose pliers
Circlip pliers
Flat Screwdriver
Chisel
Rags
Brake Fluid
Brake Cleaner
2000 grit sandpaper
High temp lithium grease or equivalent
Something plastic or wooden to remove the square seal, like a zip tie or skewer
Step 1: Unlike the front calipers, the rear piston needs to be twisted out
Using the rear piston removal tool or needle nose pliers, start turning the piston counter clockwise. At a point, the tool will bottom out and you will have to use the pliers the rest of the way
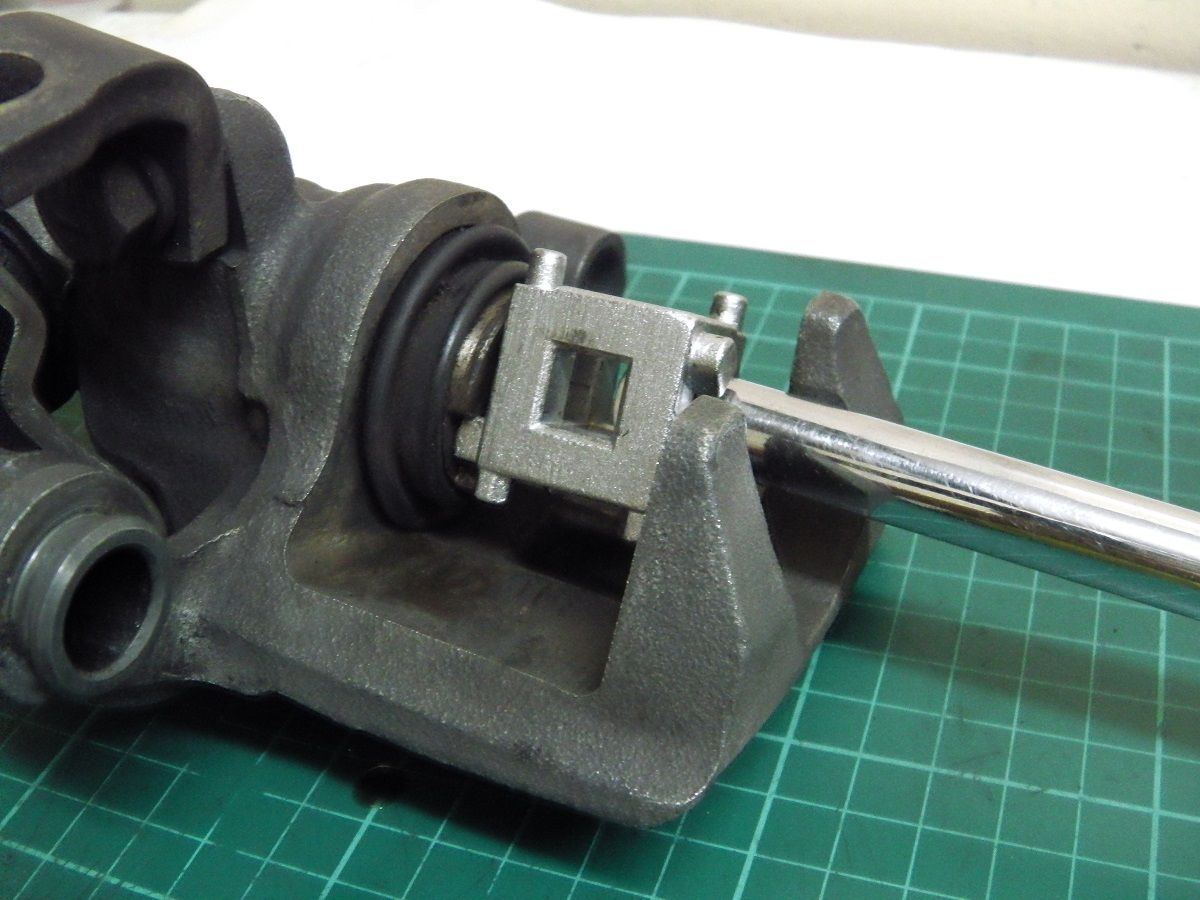

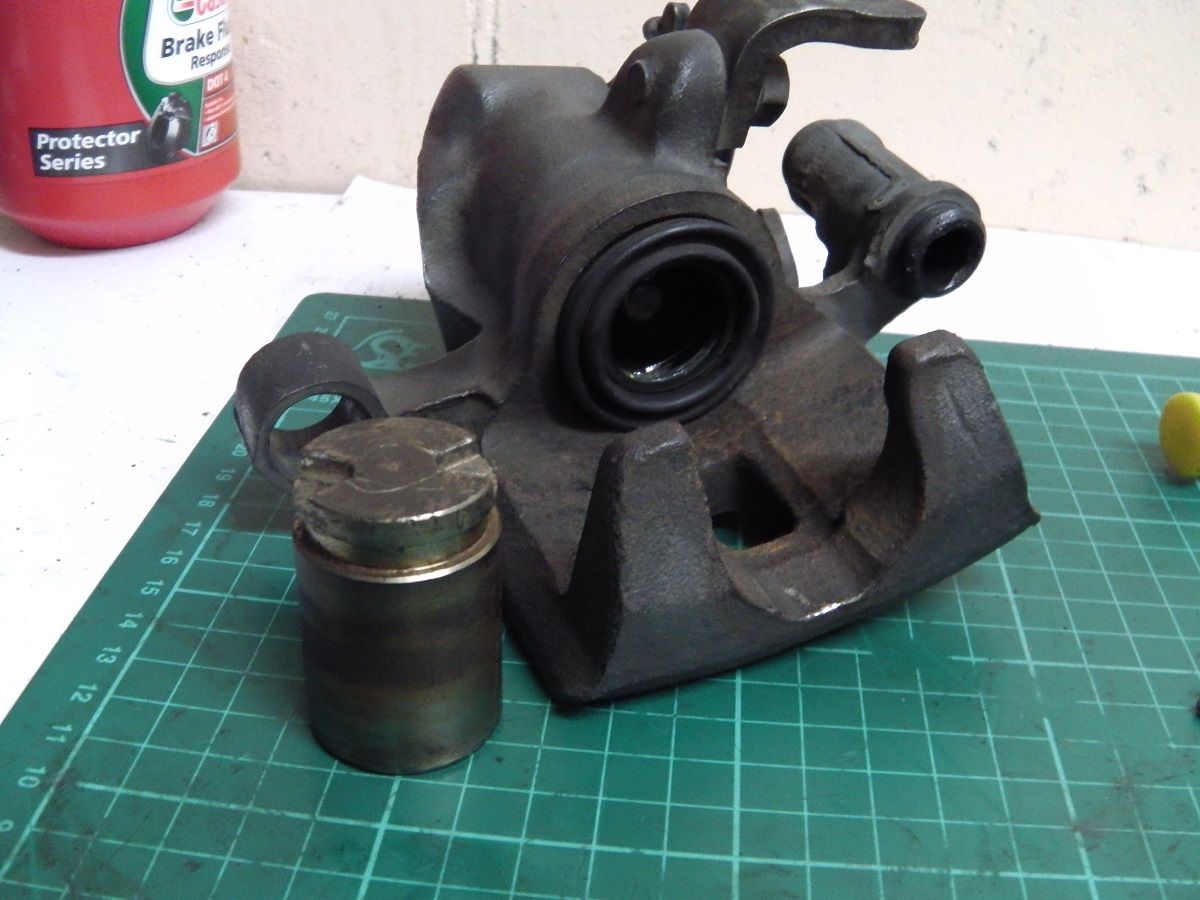
Step 2: Remove the old retaining ring that is holding the dust boot in using a flat screwdriver
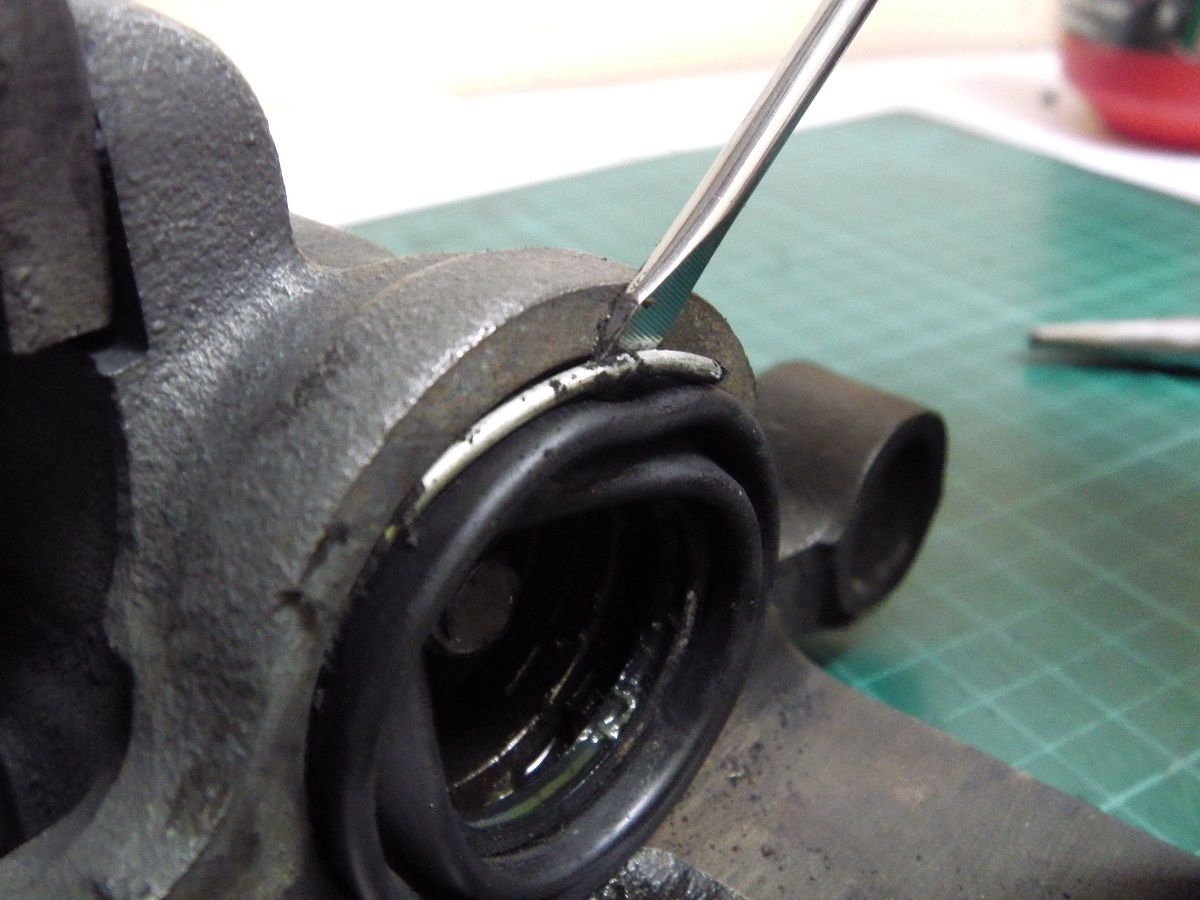
Step 3: This is the tricky part, we now need to remove the auto-adjuster spindle assembly.
There is a circlip at the bottom of the bore holding it in place. To remove the circlip, I had to use the head of my circlip pliers with a pair of needle nose pliers as the circlip pliers would not fit.
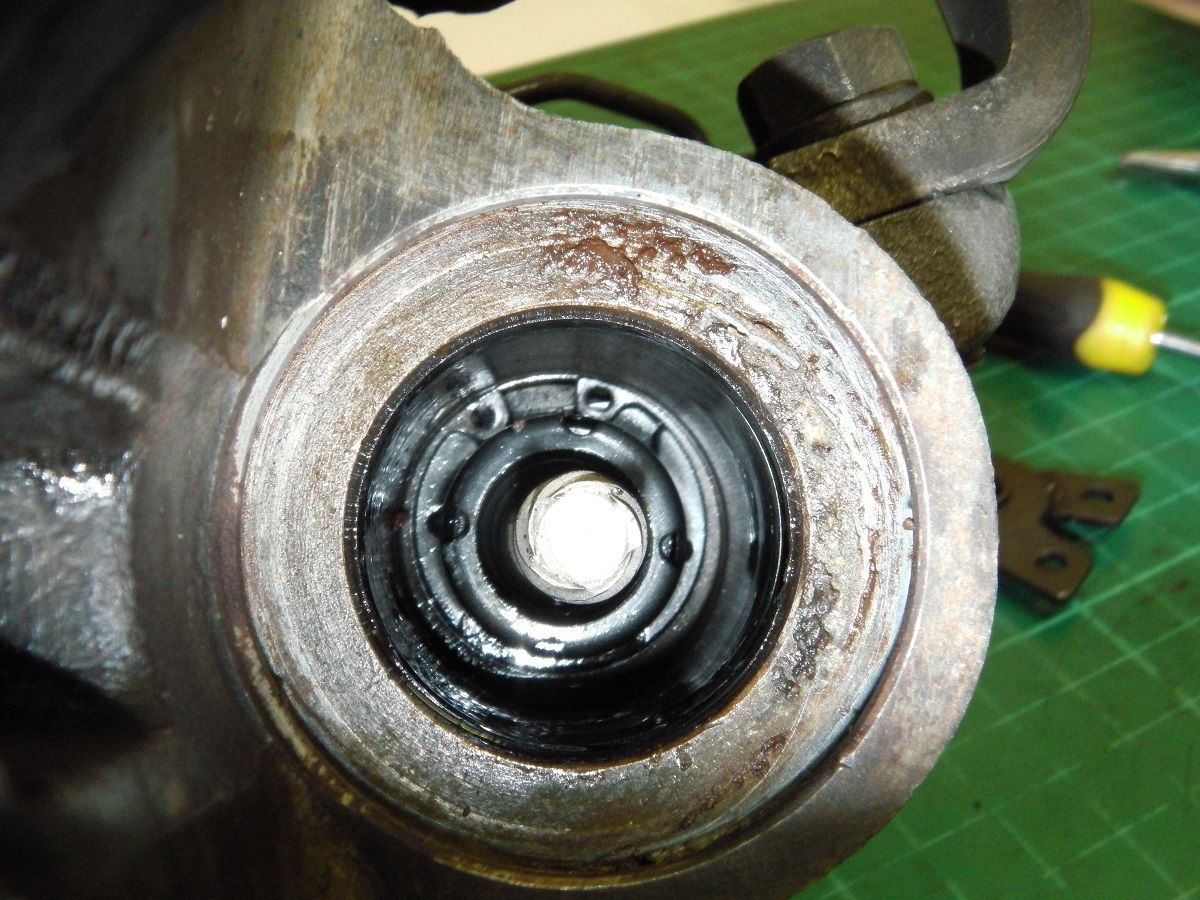
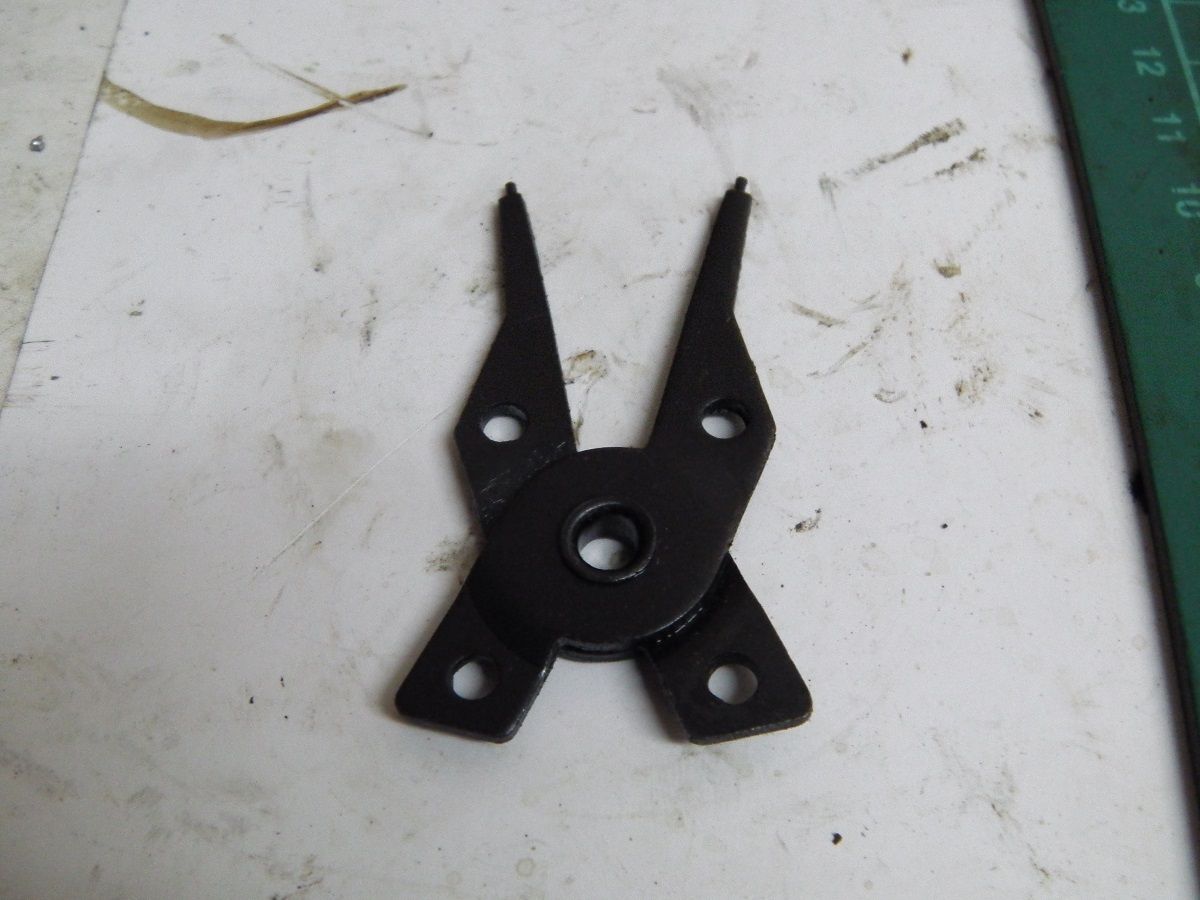
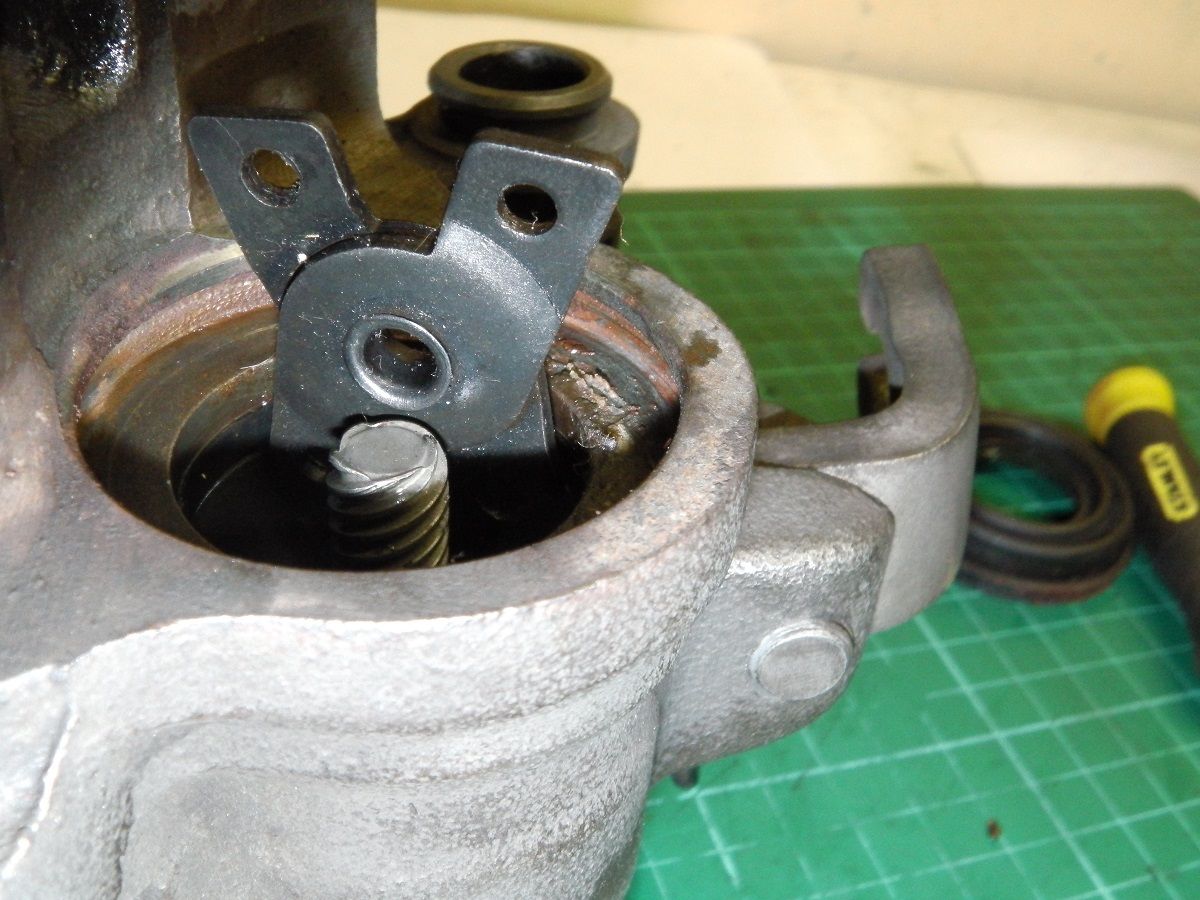
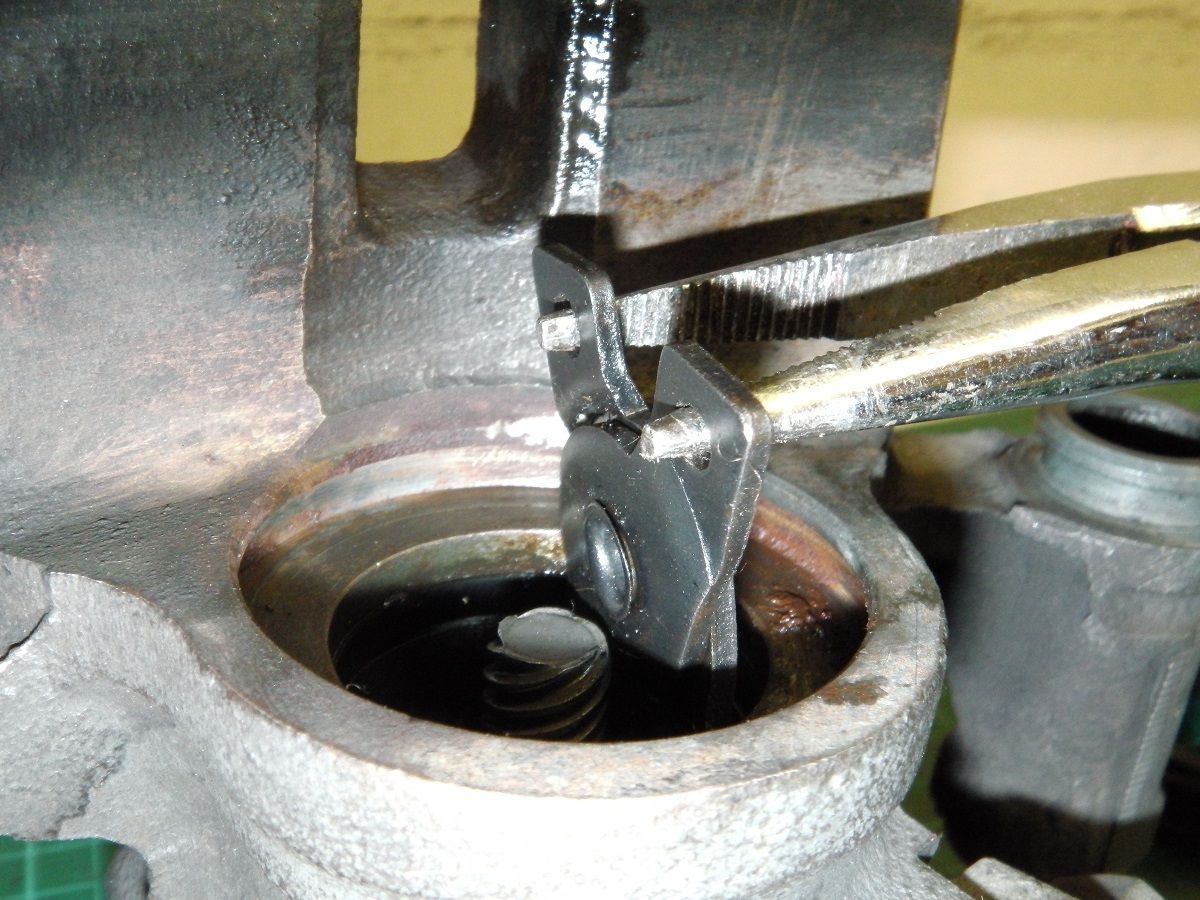
Once you have the circlip out, remove the spring case, spring and stopper plate.
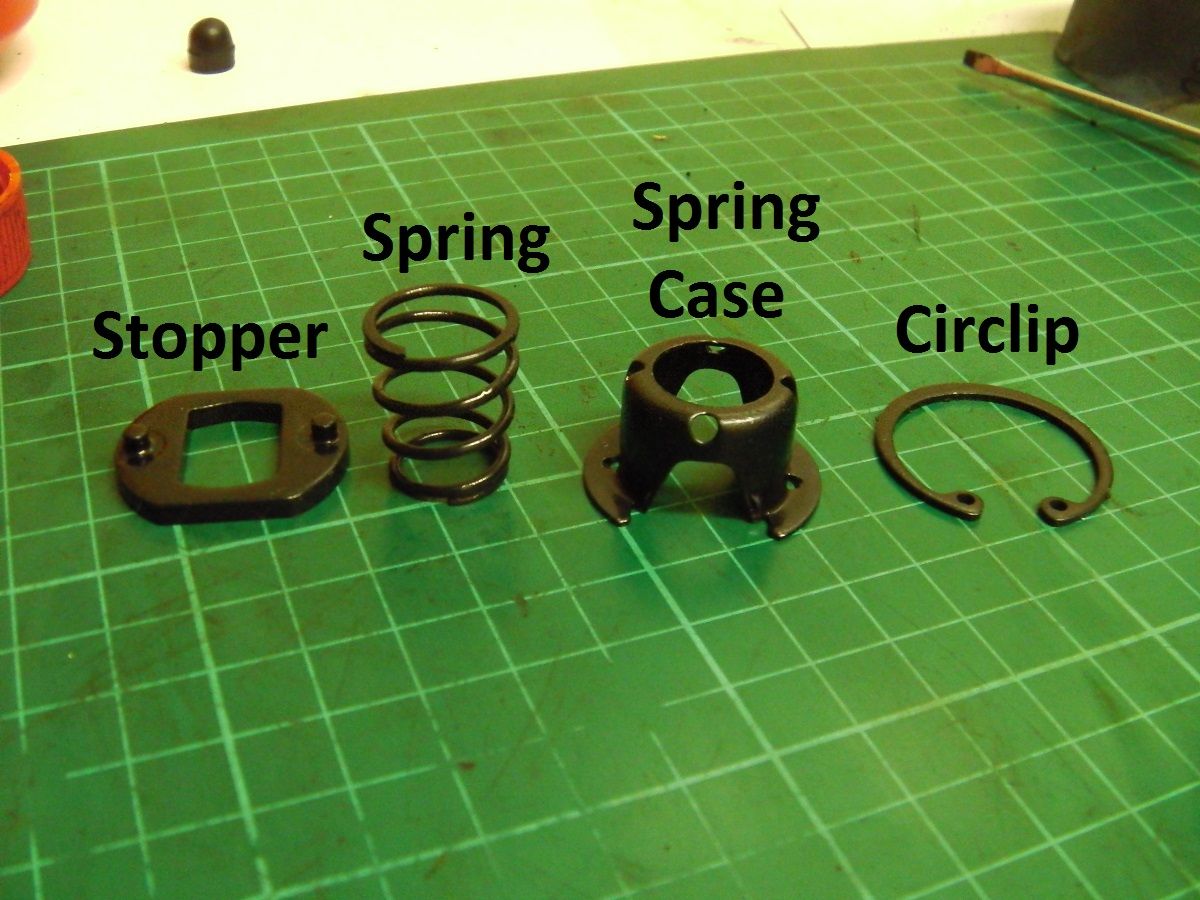
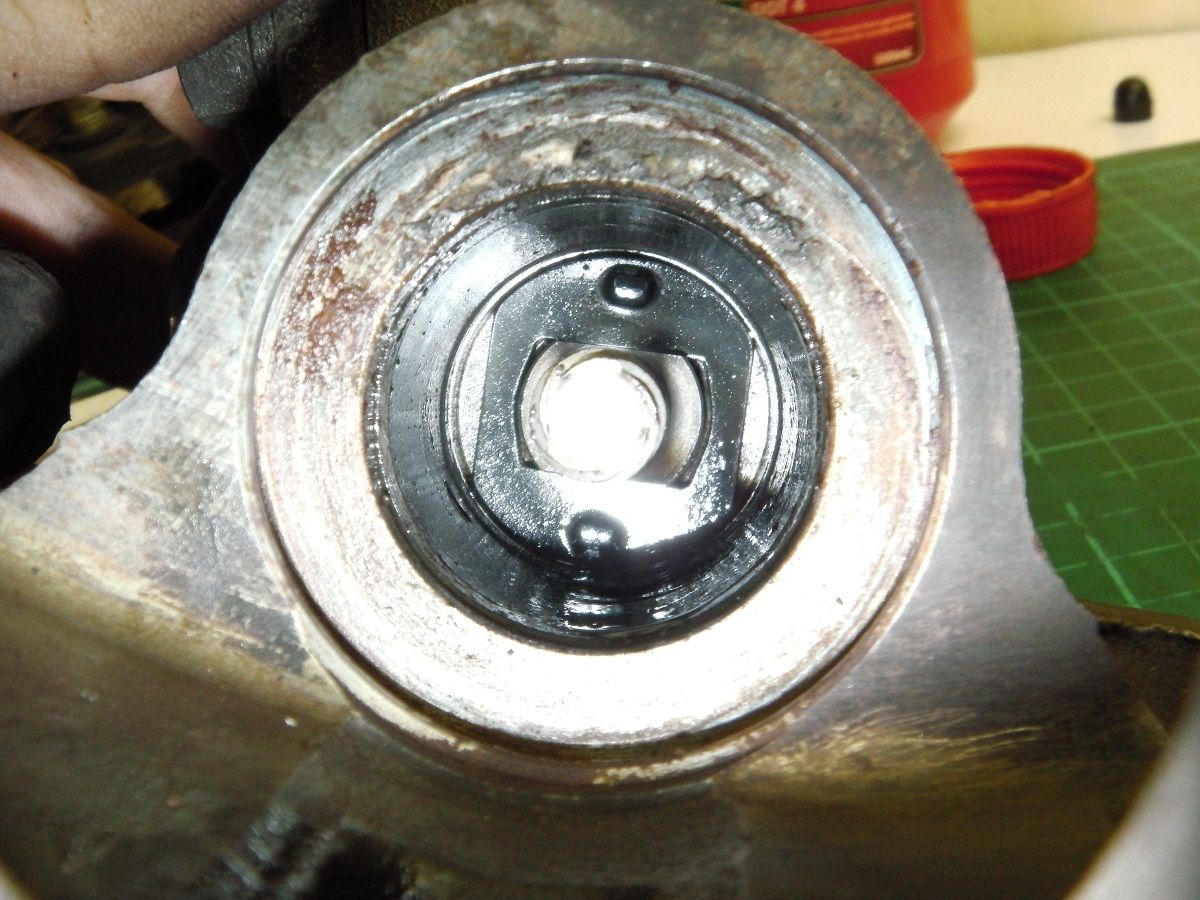
Step 4: Remove the spindle. If it is a little stuck, screw the piston back on a few turns and use it to pull the spindle out. There is also a small connecting pin between the spindle and spindle lever, be sure not to lose this.
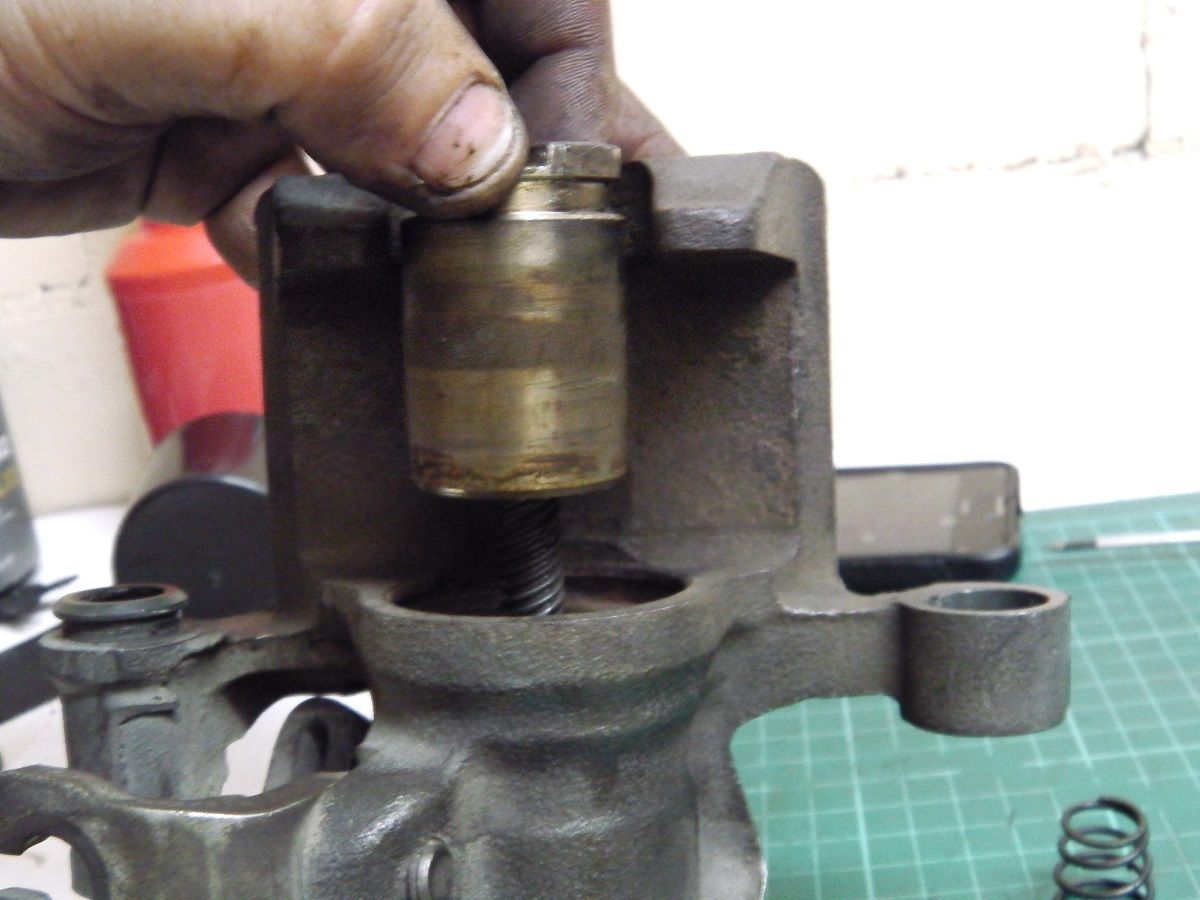
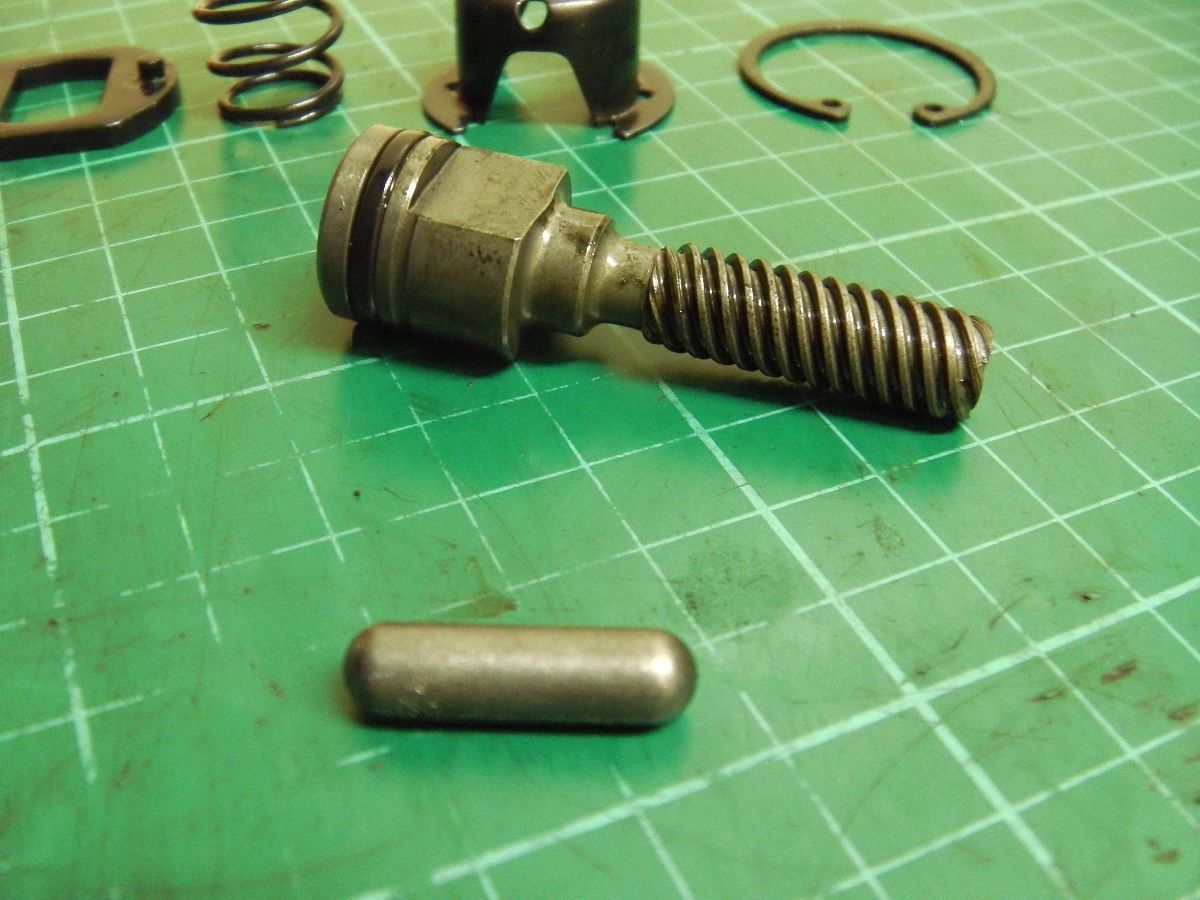
Step 5: Using a skewer or zip tie, remove the old square seal from the caliper. The reason you don't use a screwdriver or anything metal is because you don't want to scratch the inside of the caliper.
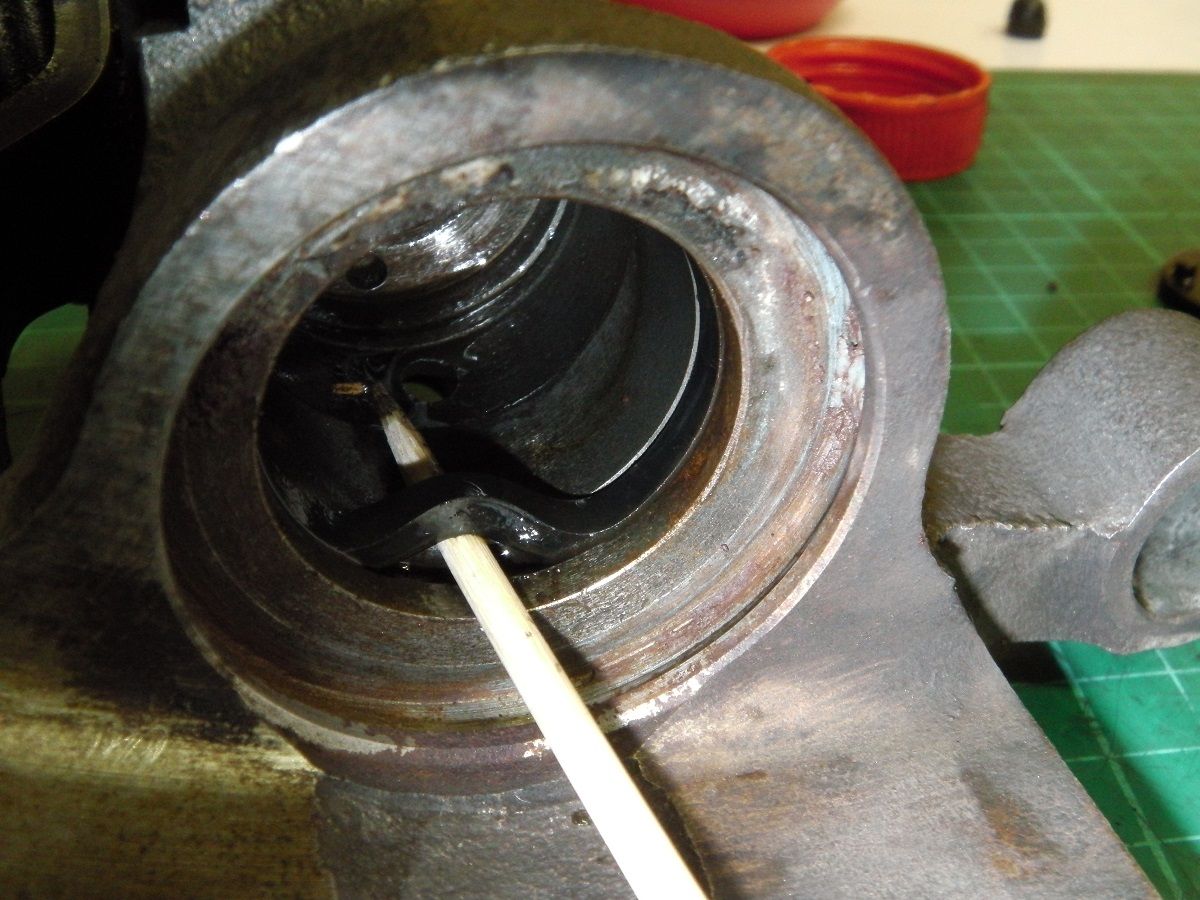
Step 6: Spray some brake cleaner on the piston and wipe it with a rag to clean off any solidified brake fluid/contaminants. If there is minor pitting on it, you can use some 2000 grit sandpaper to remove it.
If there is major pitting on the piston then you will need to get a replacement.
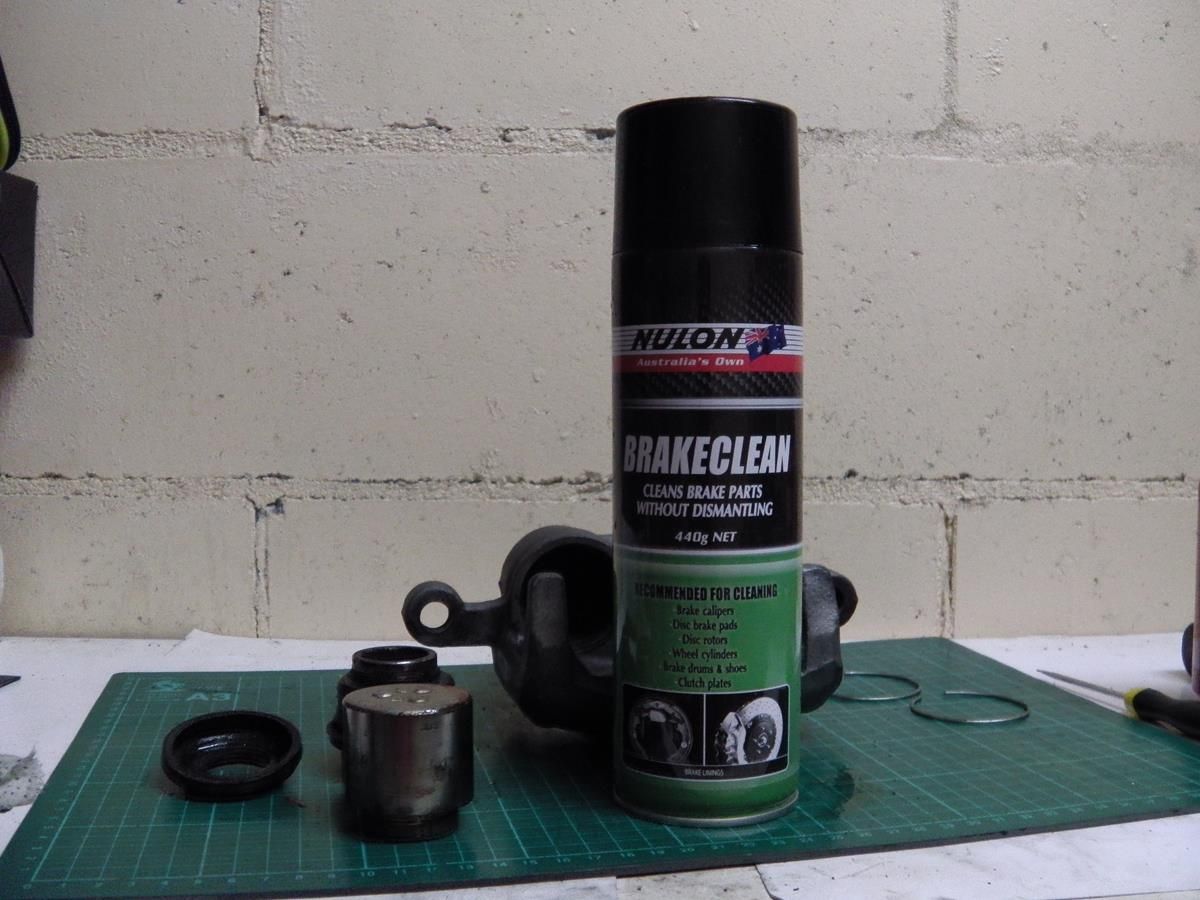
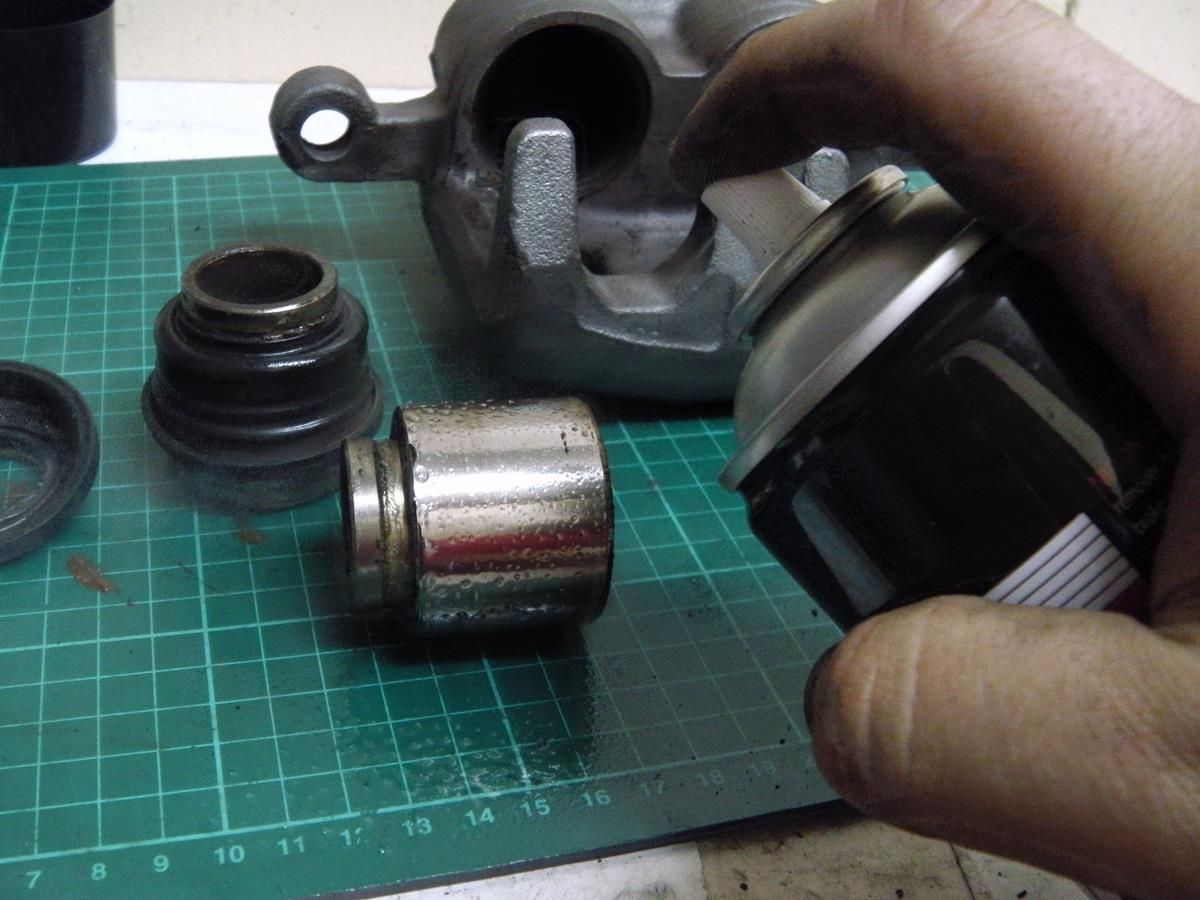
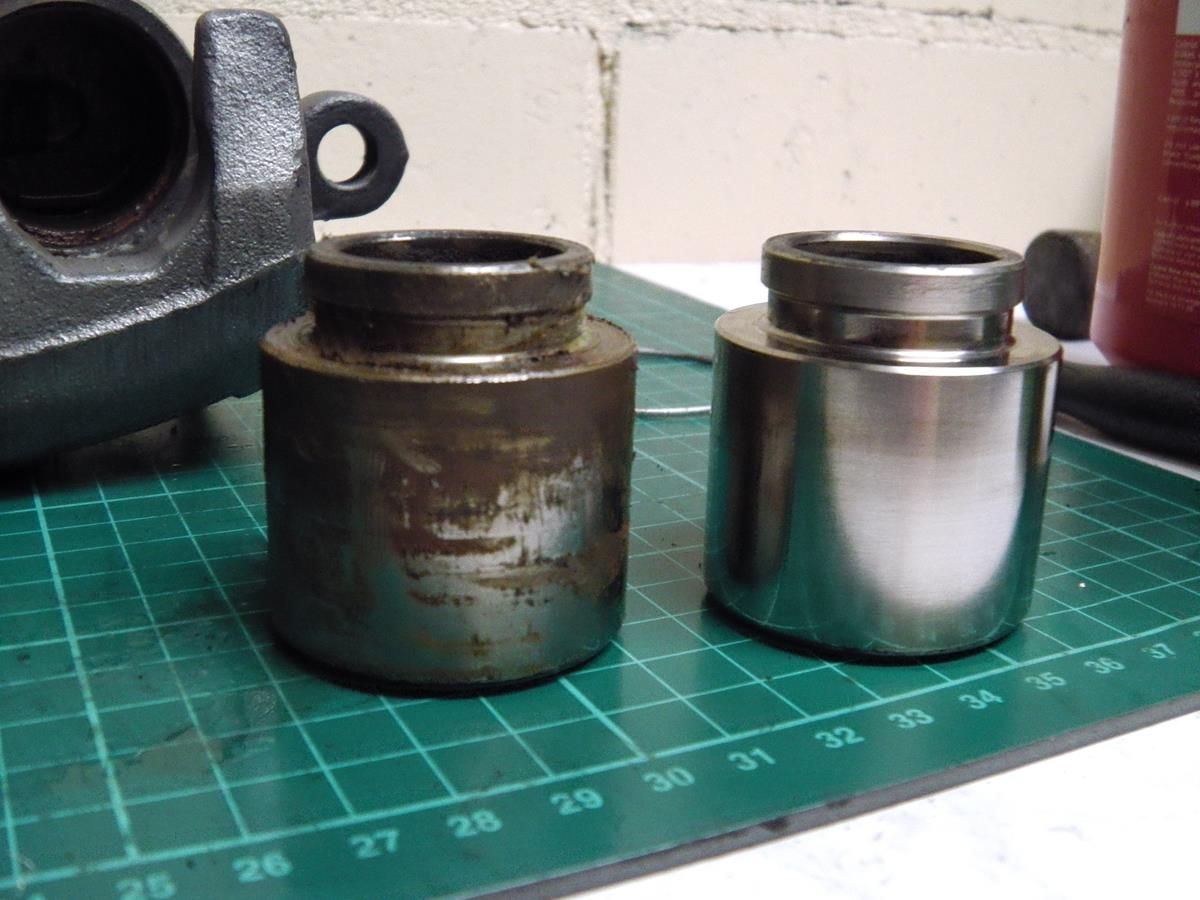
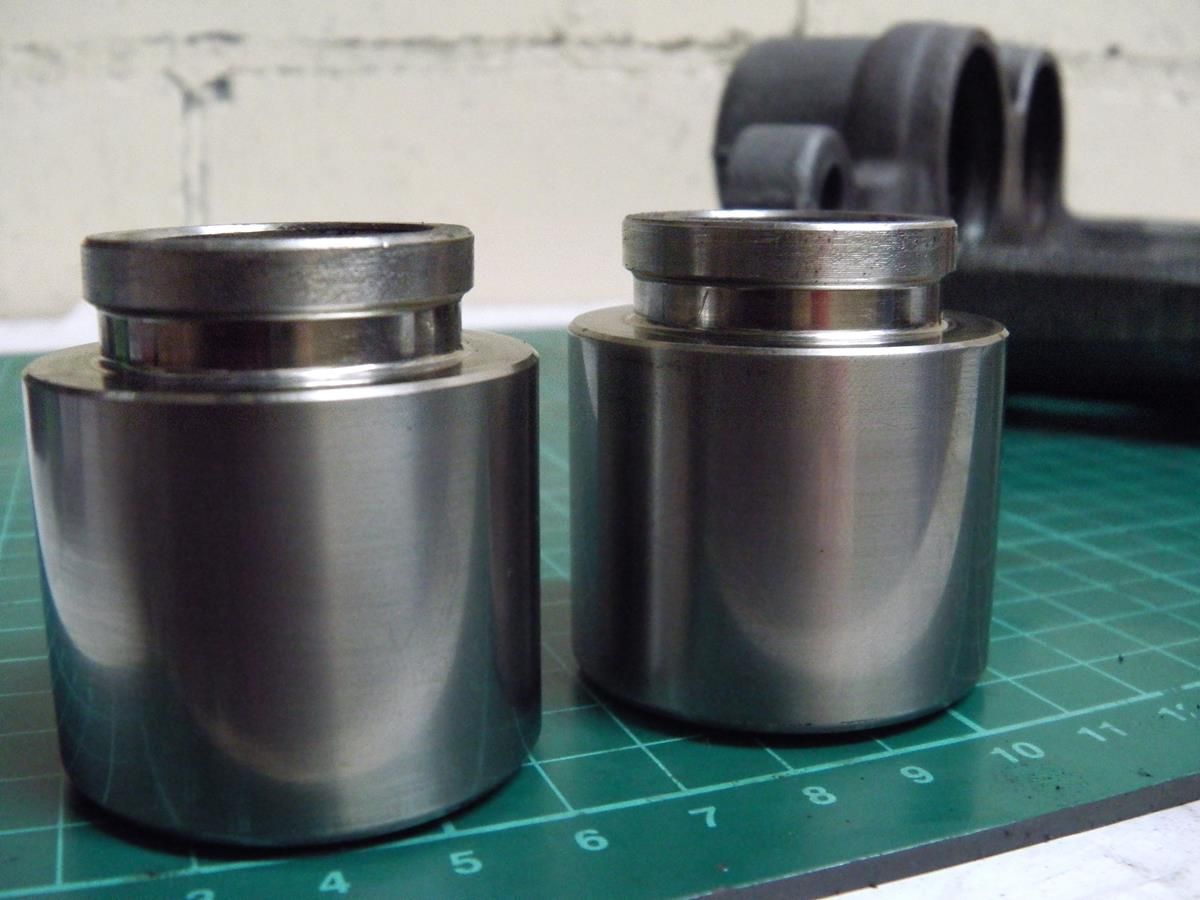
Step 7: Remove the handbrake return spring. Once it is removed the spindle lever will simply pull out. There is no need to remove the nut unless you are removing the bracket from the lever.
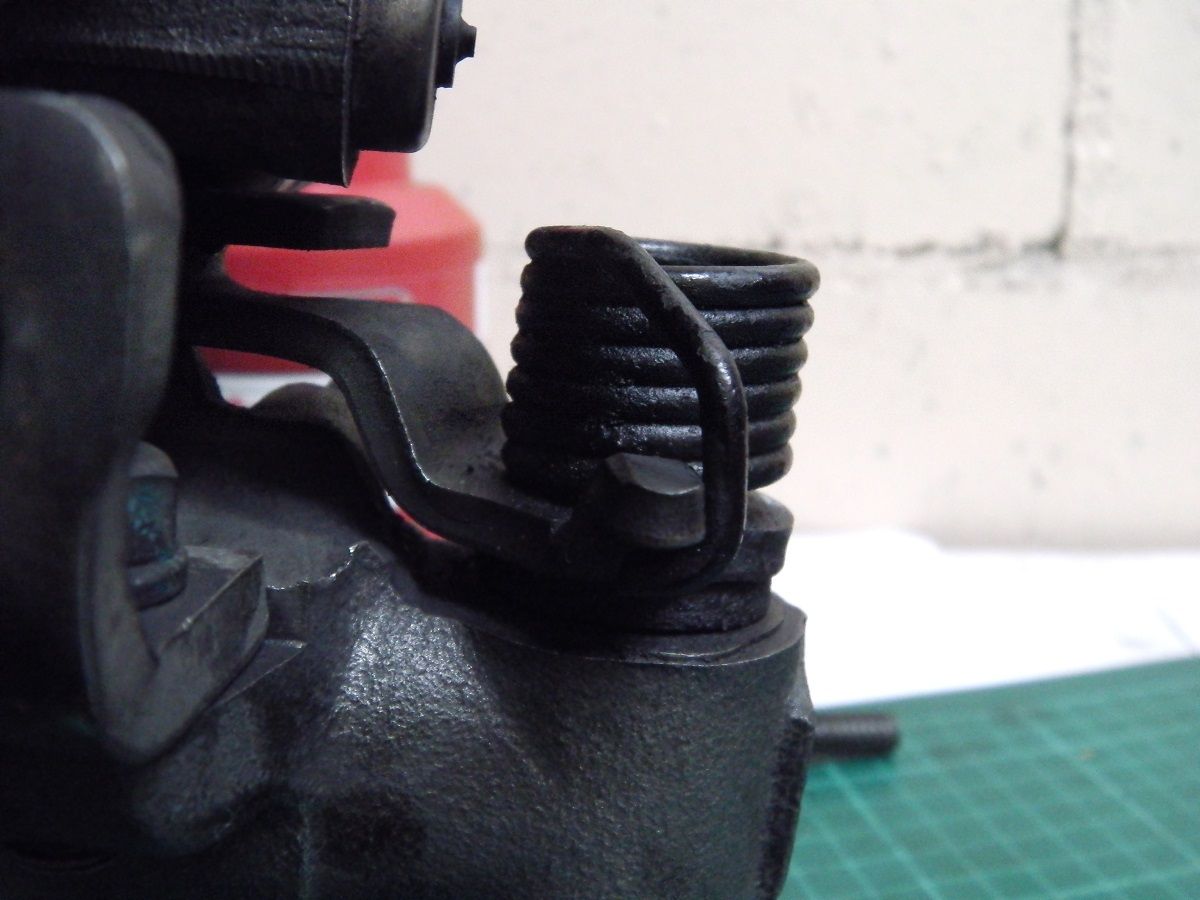
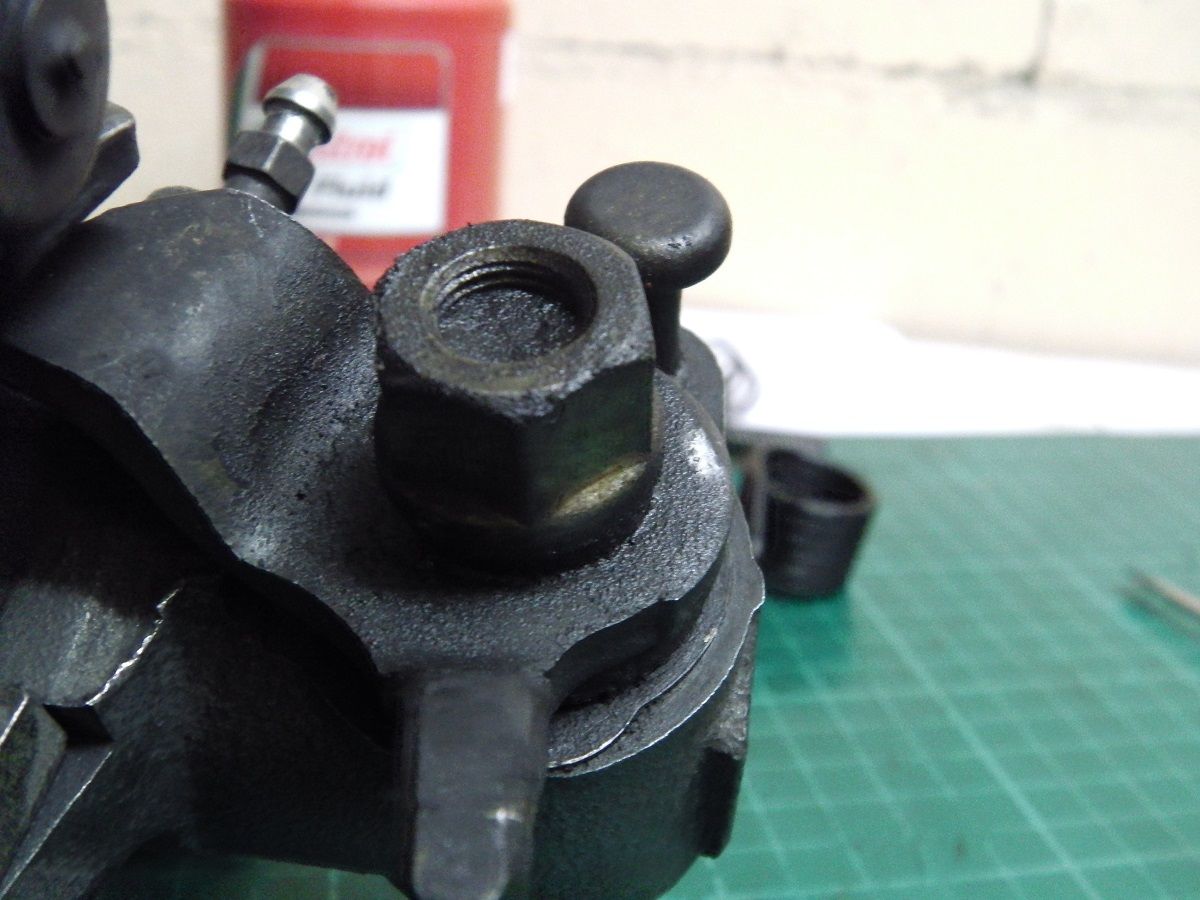
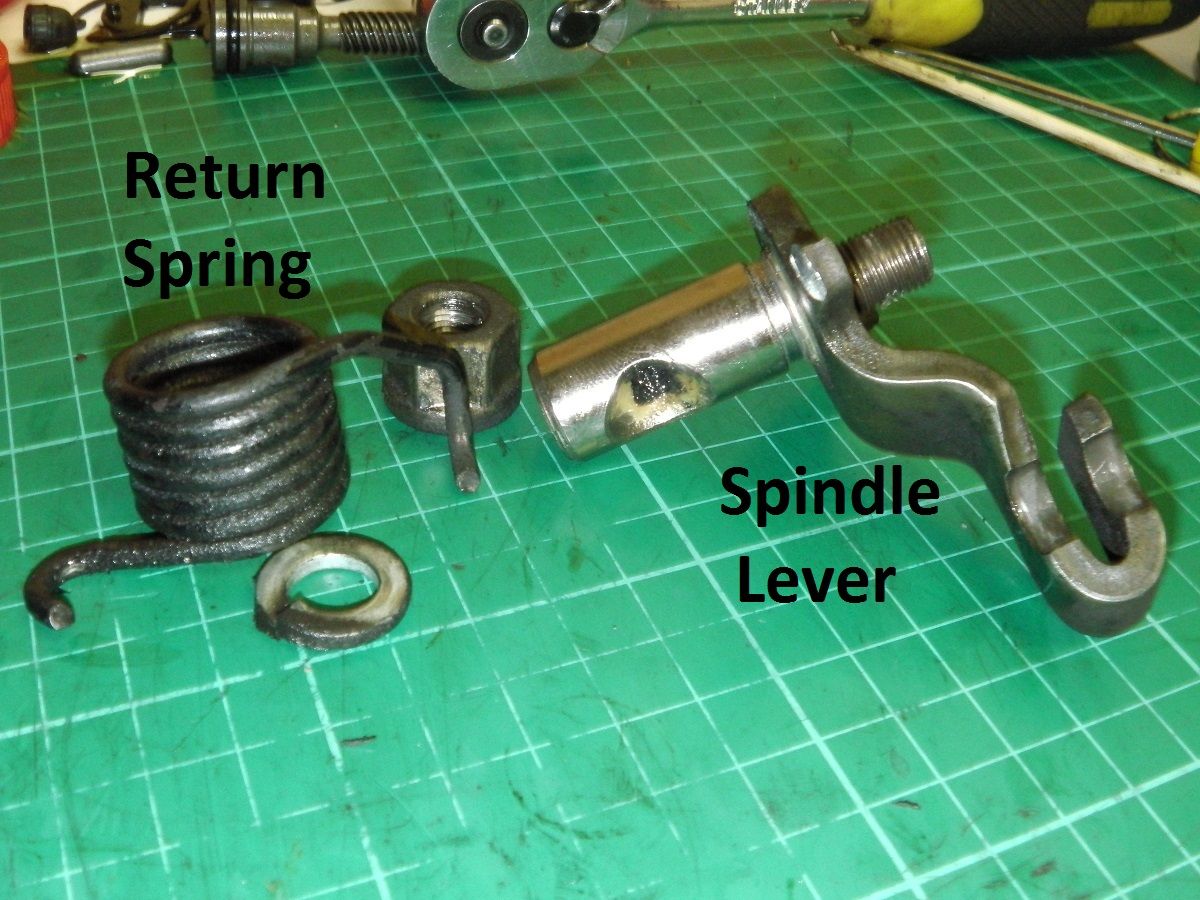
Step 8: Using a flat screwdriver or chisel, remove the seal that sits around the lever as shown.
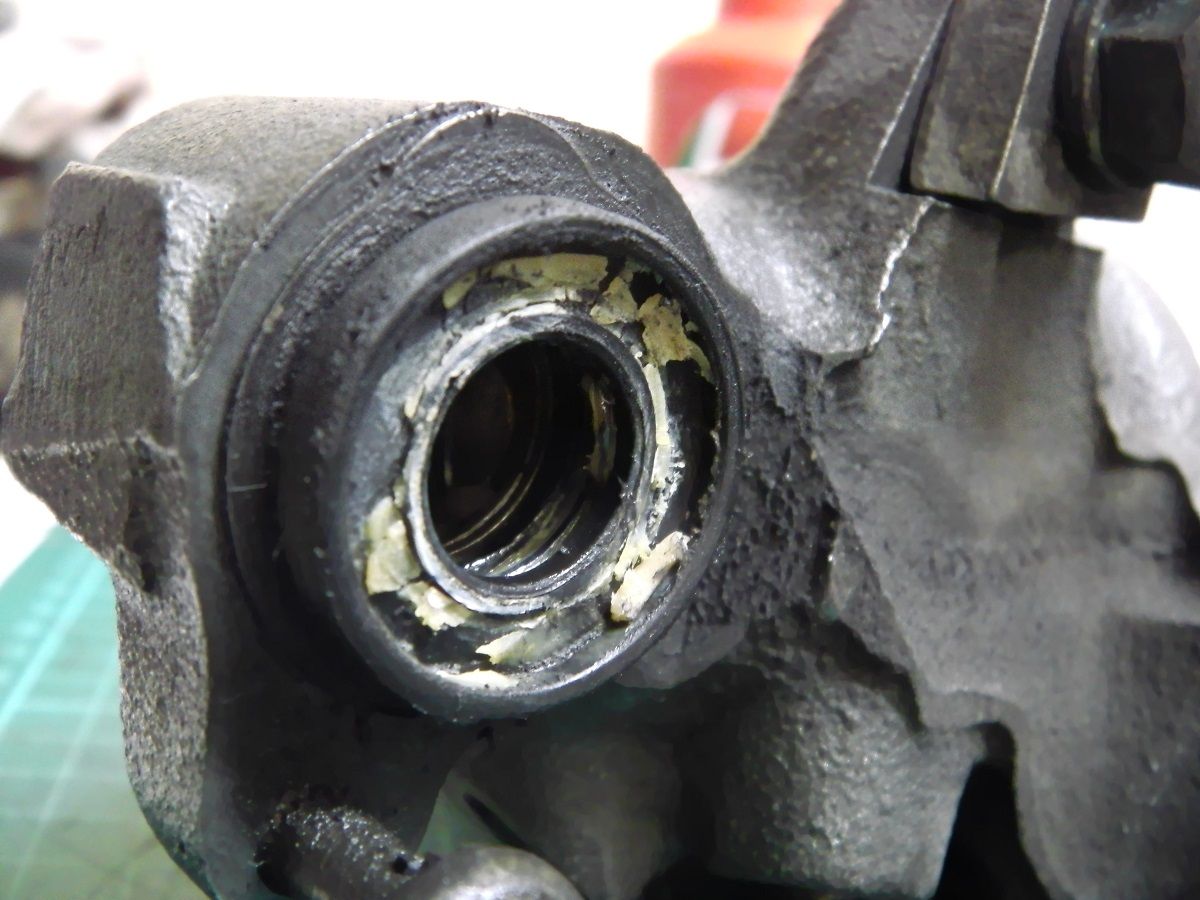
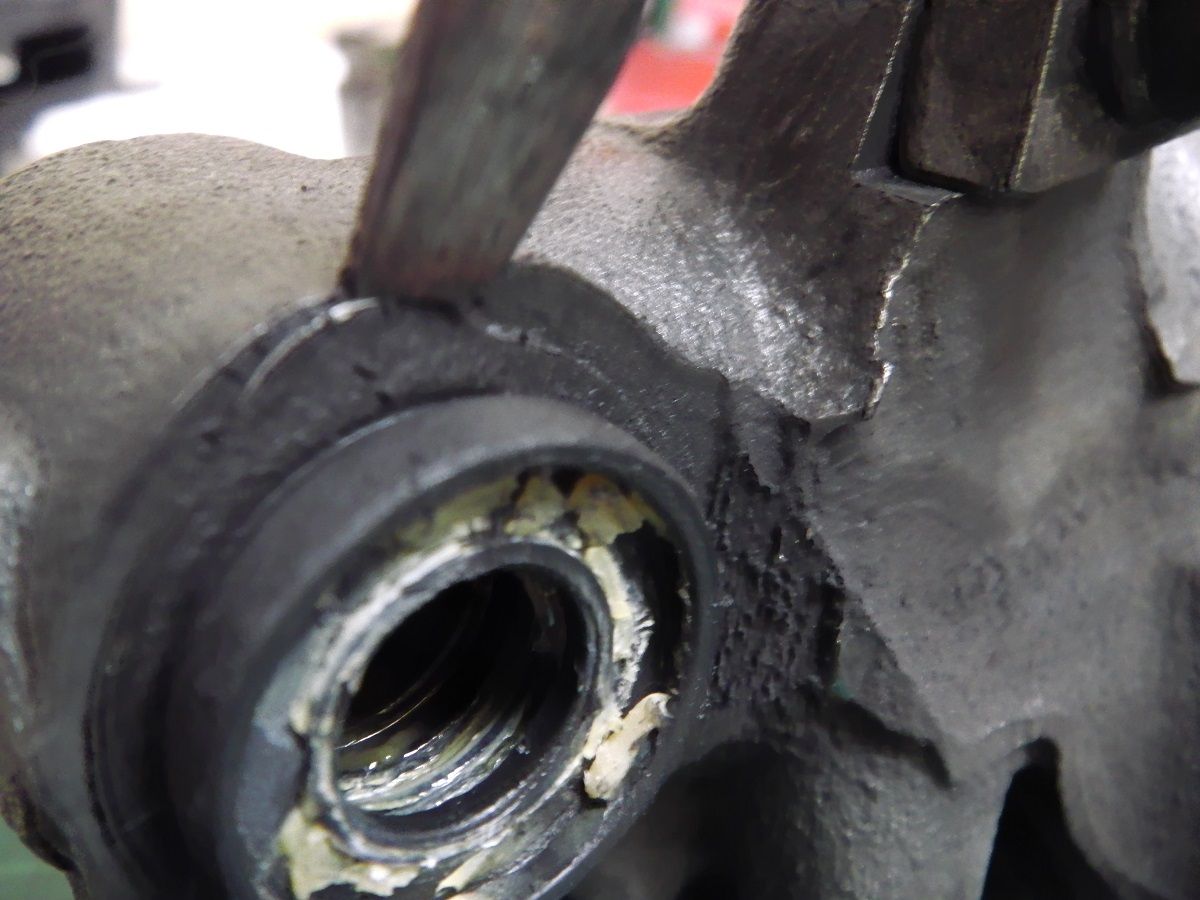
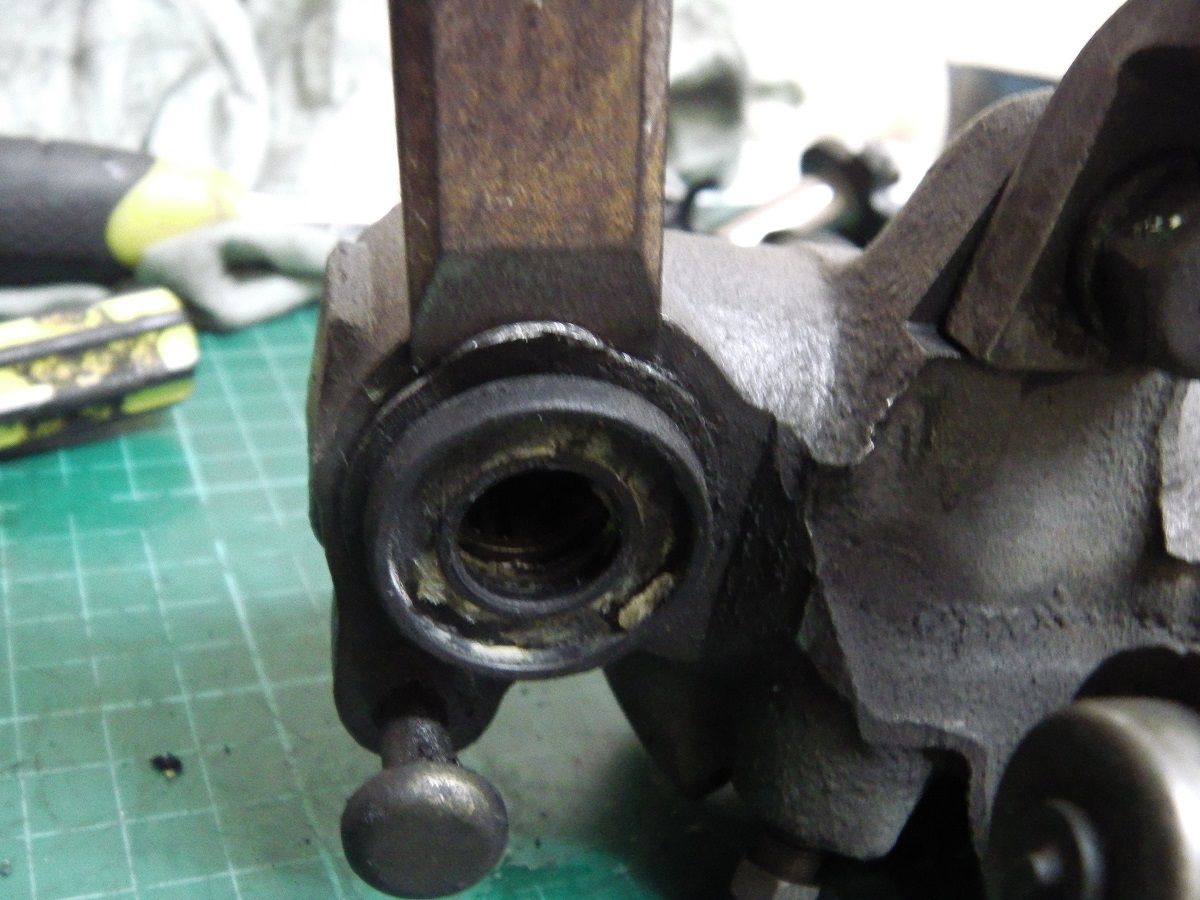
Step 9: Give the inside of the caliper a good clean with some brake cleaner. Spraying inside the bore and inside where the spindle lever sits, make sure to clean out all grease from the spindle lever bearing.
Remove any corrosion in the cylinder bore using some 2000 grit sand paper. You won't be able to get it completely clean but as long as it feels smooth it should be good.
Give it another spray with brake cleaner and make sure the seal groove is completely clean.
Re-grease the spindle lever bearing.
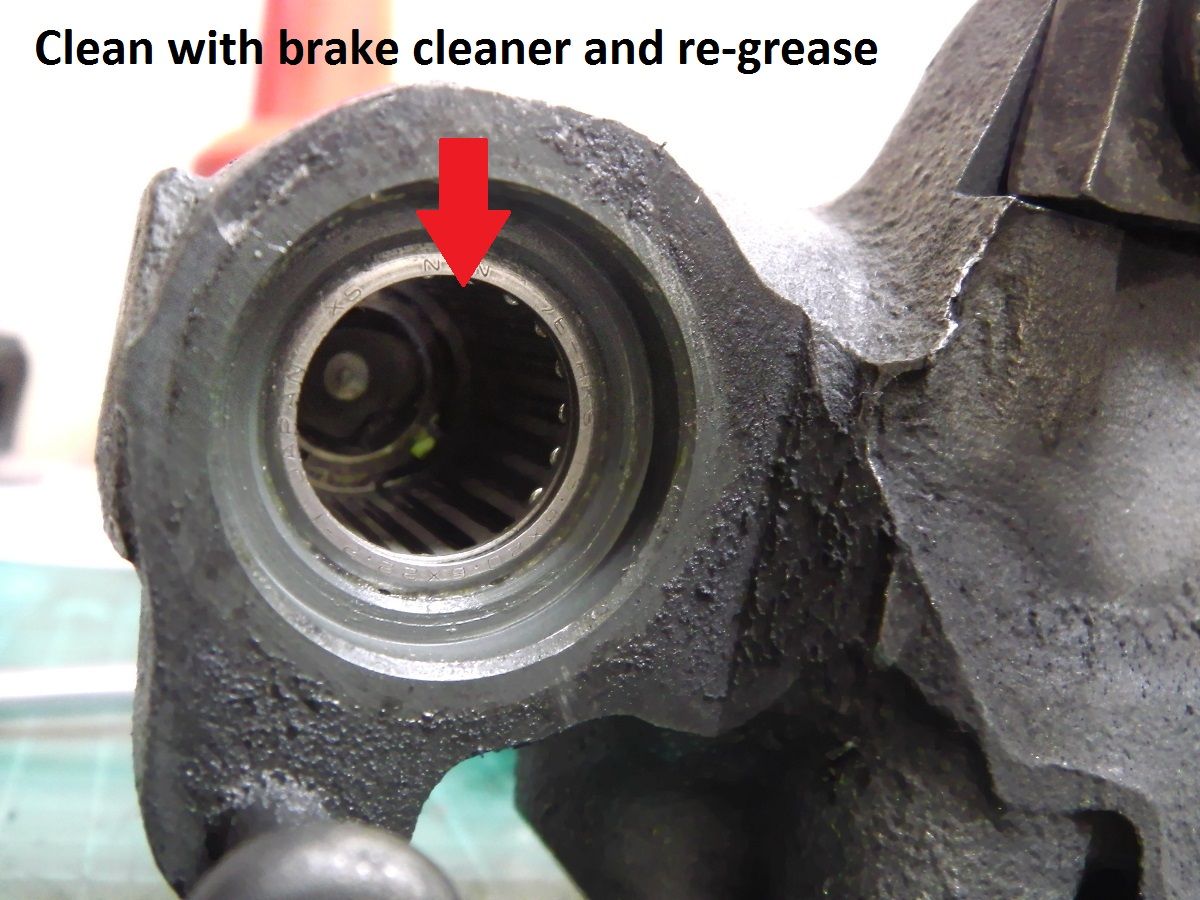
Step 10: Now we need to press in the new spindle lever seal, the easiest way to do this is using a socket that fits around the rubber part of the seal and using a hammer, tap it in.
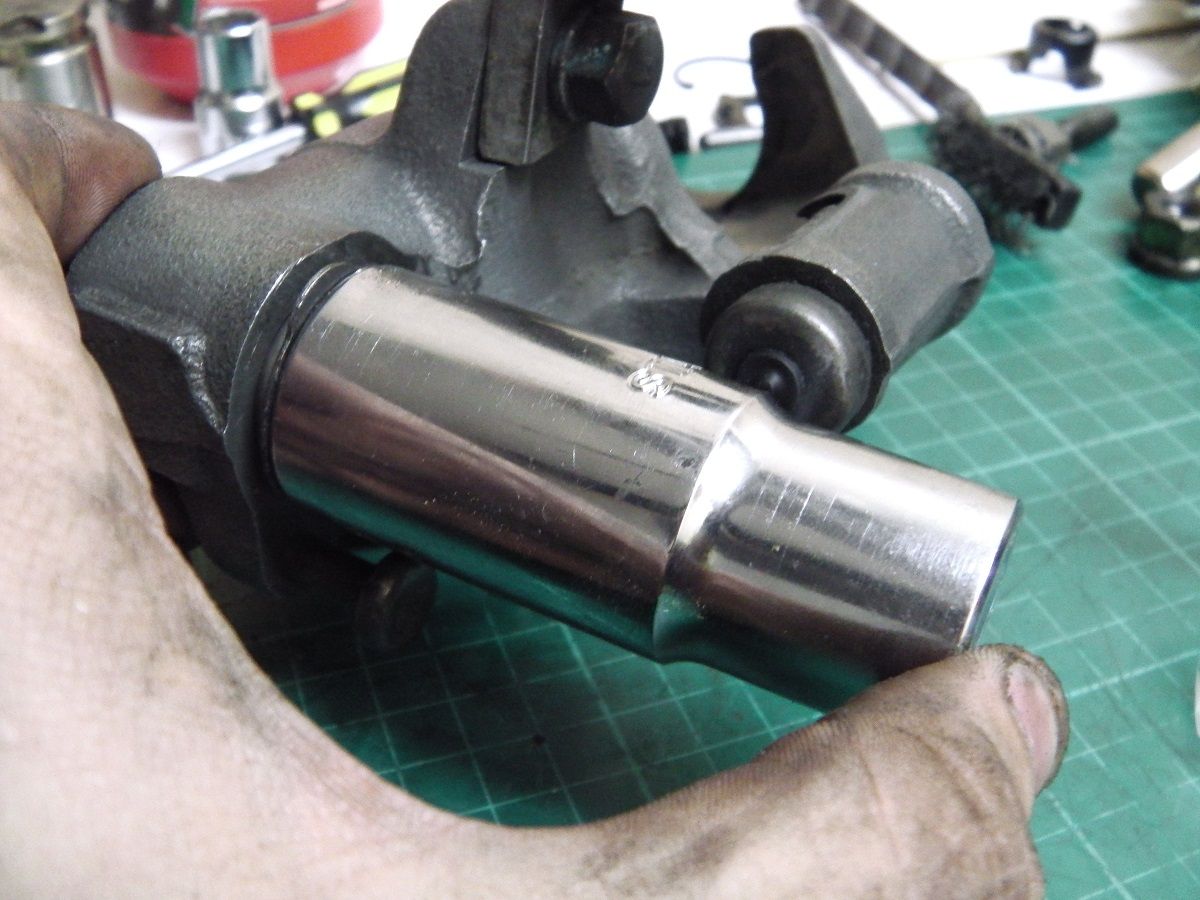
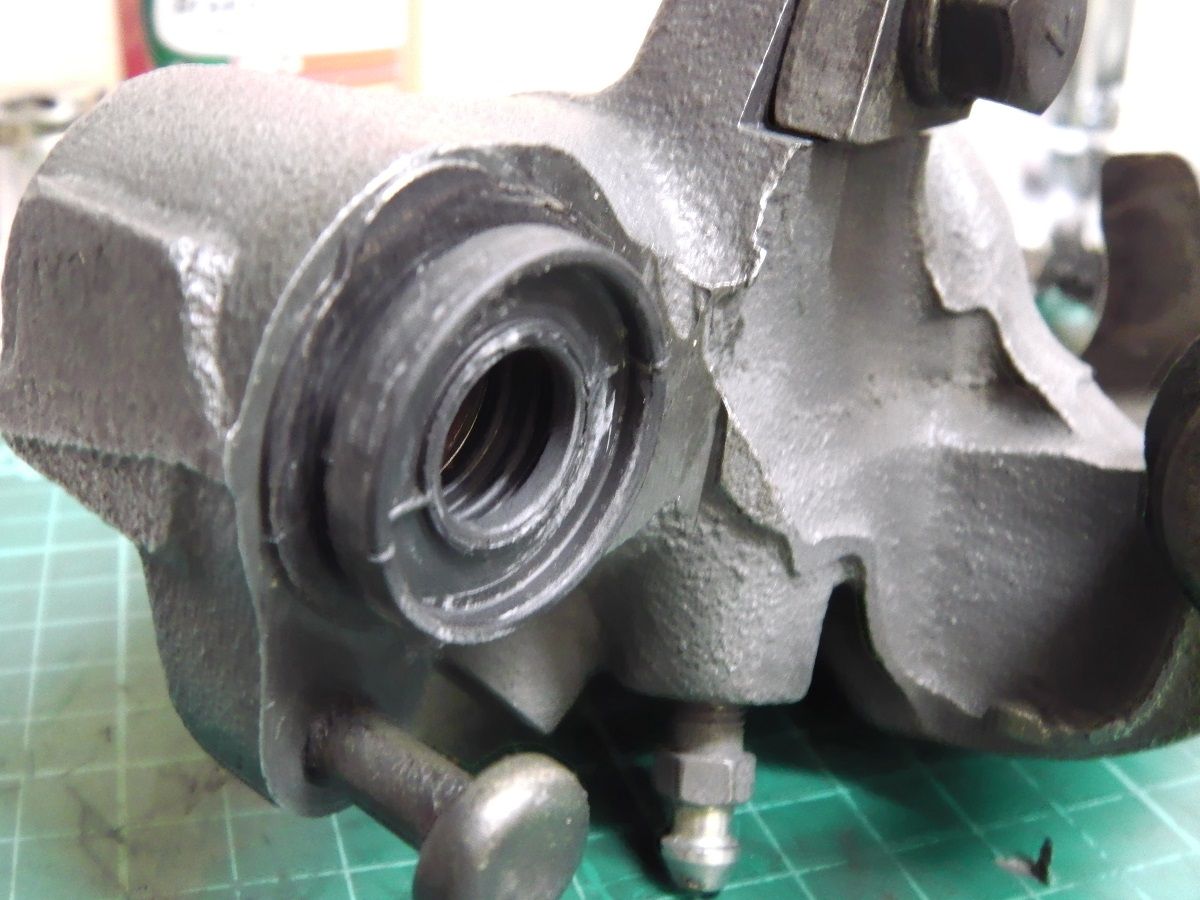
Step 11: You may want to put on some nitrile gloves for this.
Apply some brake fluid to the cylinder bore and the square seal. I like to pour some brake fluid in the cap and spin the seal around in it.
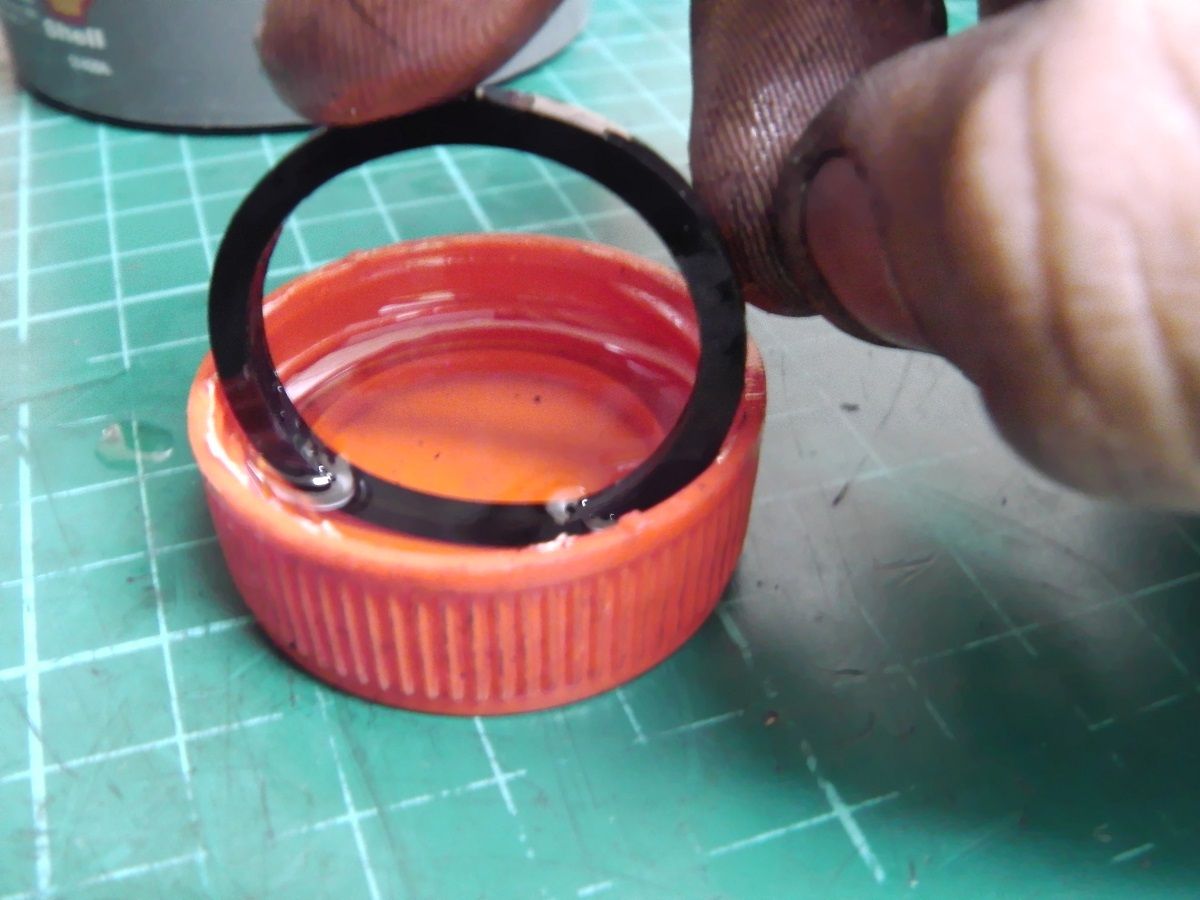
You should also not stick your fingers into the brake fluid bottle if you plan on using it to top up your cars fluid as you may contaminate it.
Step 12: Install the seal into the caliper, making sure there are no twists in it.
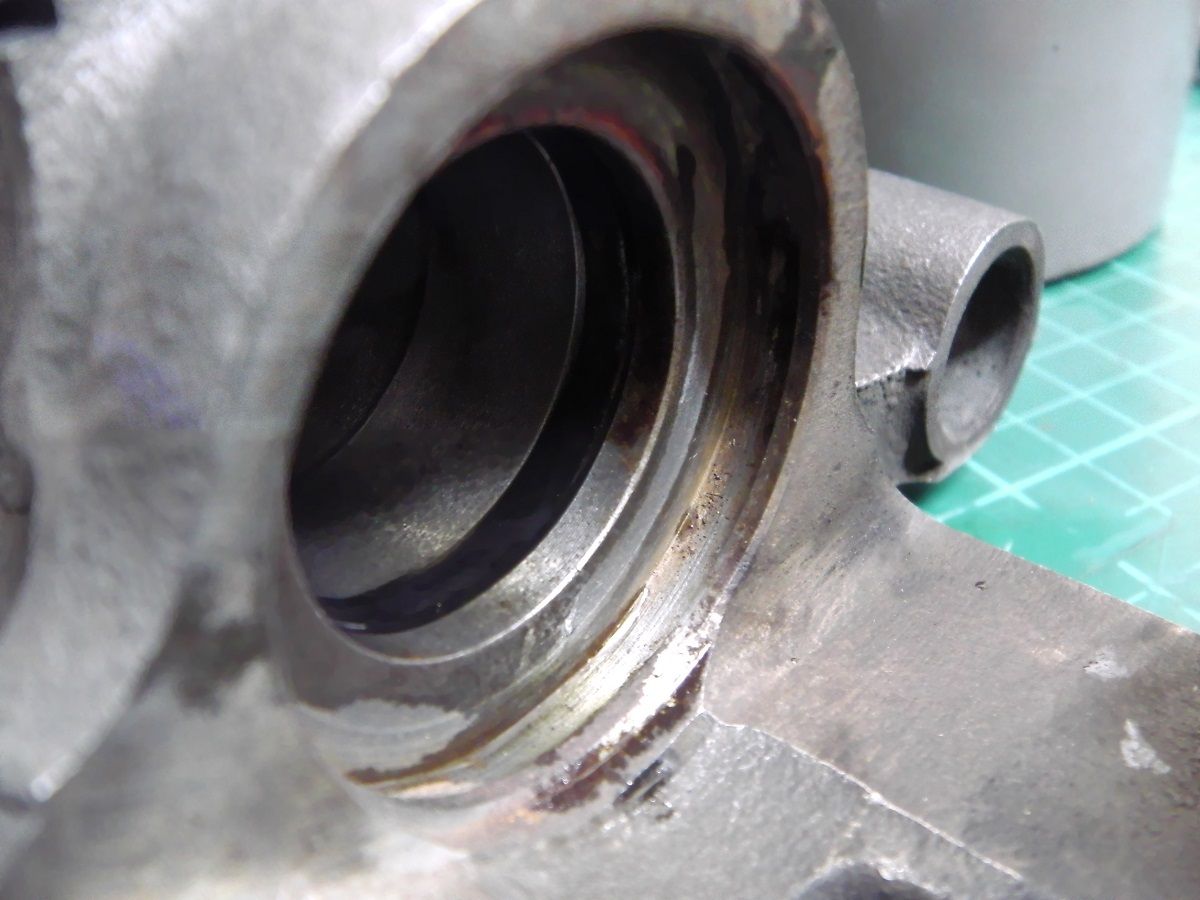
Step 13: Replace the O Ring on the spindle.
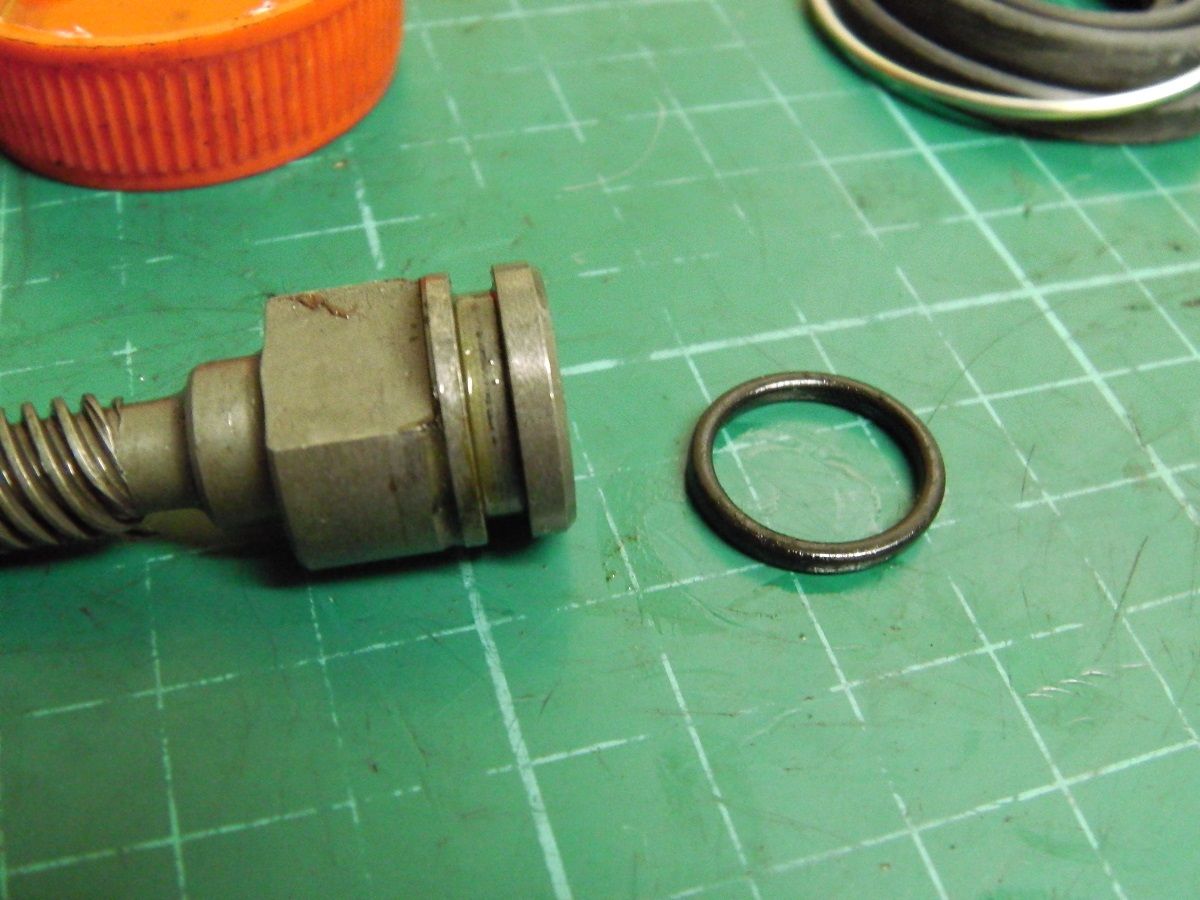
Step 14: Apply grease to the spindle lever and insert it back in to the caliper, making sure the hole for the connecting pin is pointing up towards the bore. The bearing also has a cutout in it, which also needs to be oriented towards the bore.
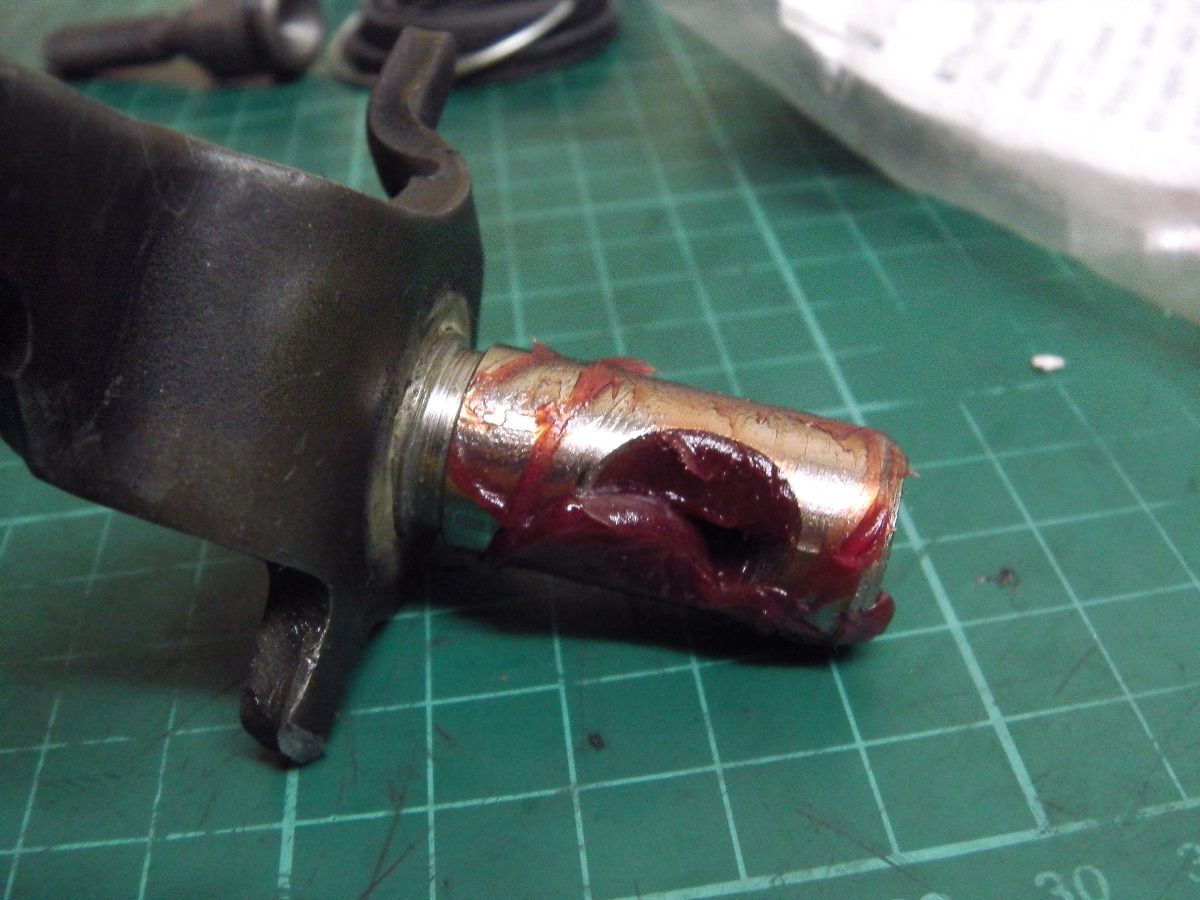
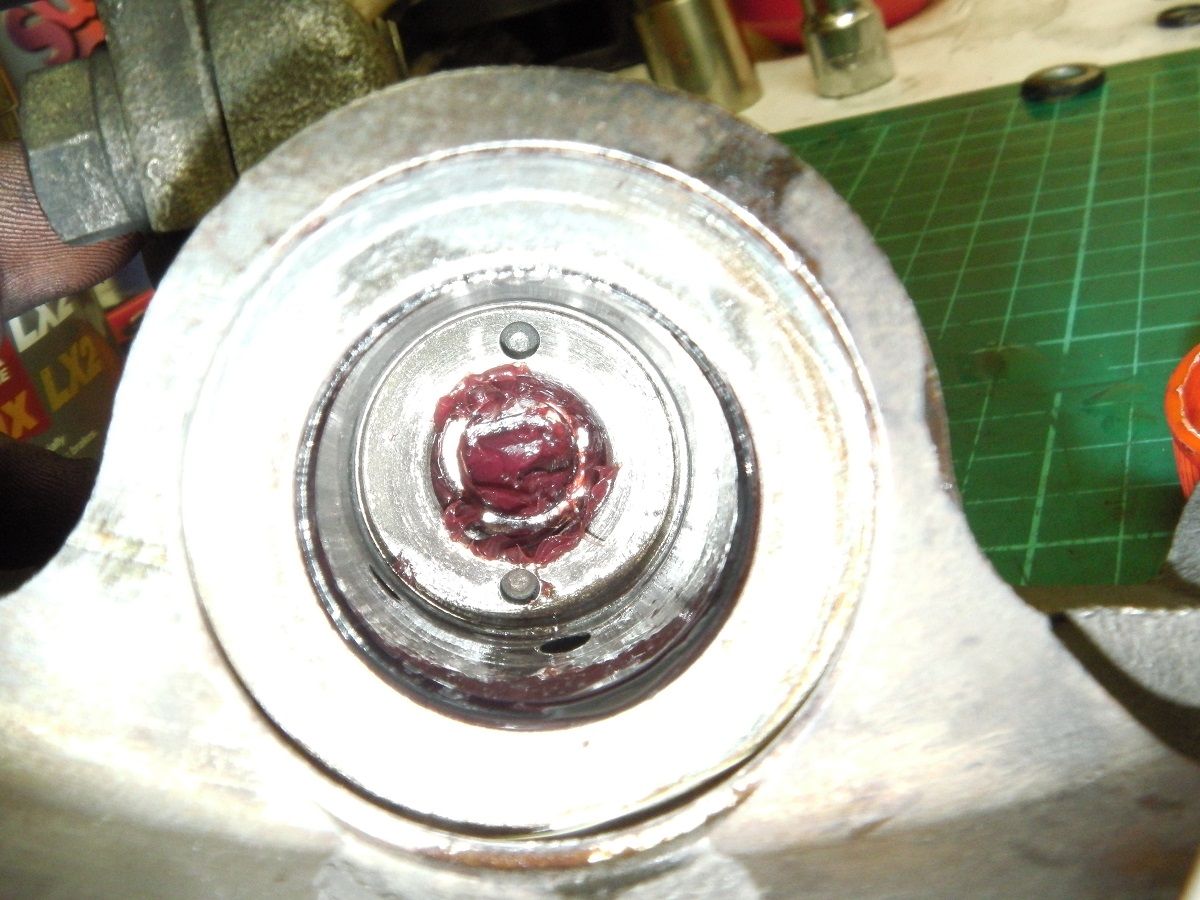
Step 15: Attach the return spring and nut (if removed)
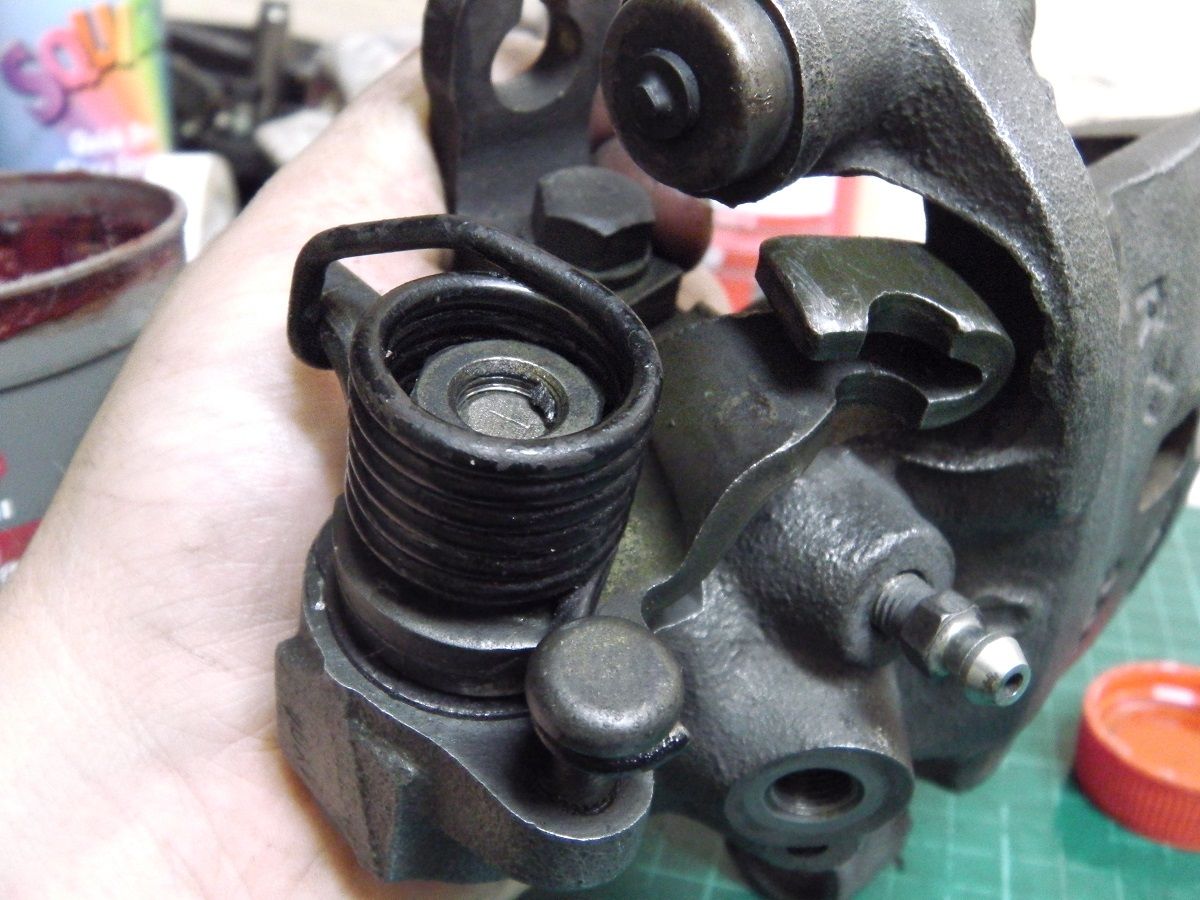
Step 16: Grease the connecting pin and the end of the spindle and insert it into the caliper, making sure the pin seats into the hole on the lever.
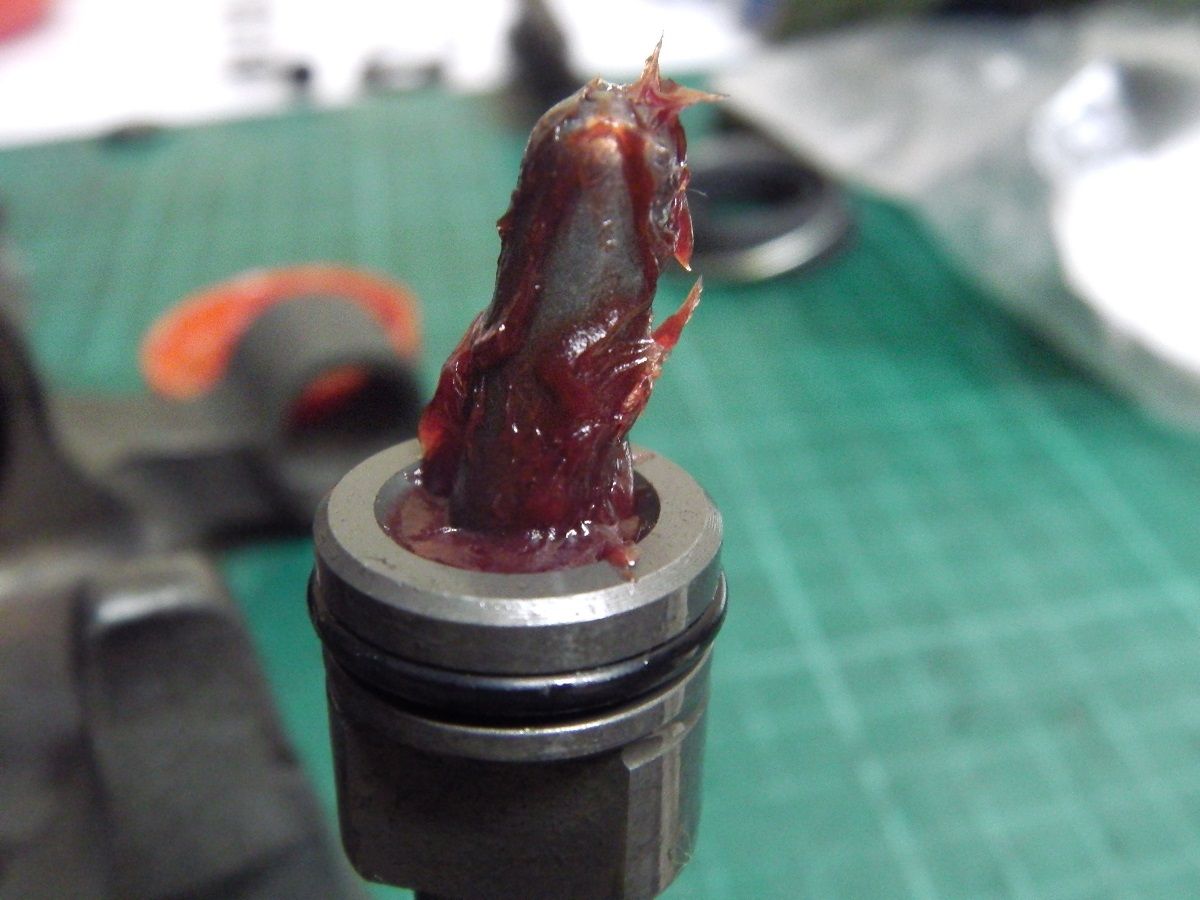
Step 17: Now this is the really tricky part, reinstalling the spring and circlip.
The parts are assembled in the same order as shown in the photo.
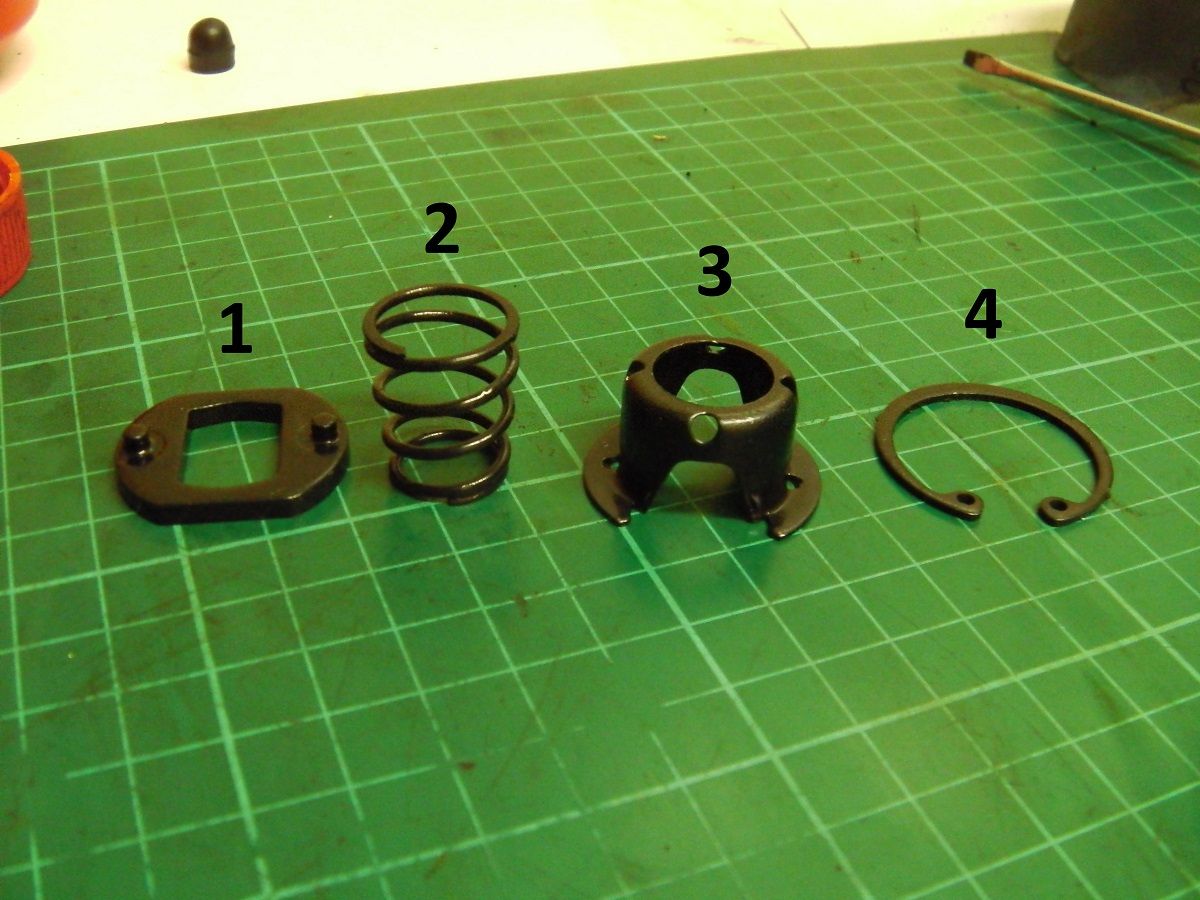
The stopper plate needs to go in with the pins facing down and they need to seat in the holes, you may need to spin the spindle around a bit to get it seated properly.
The spring goes in with the narrow side facing down.
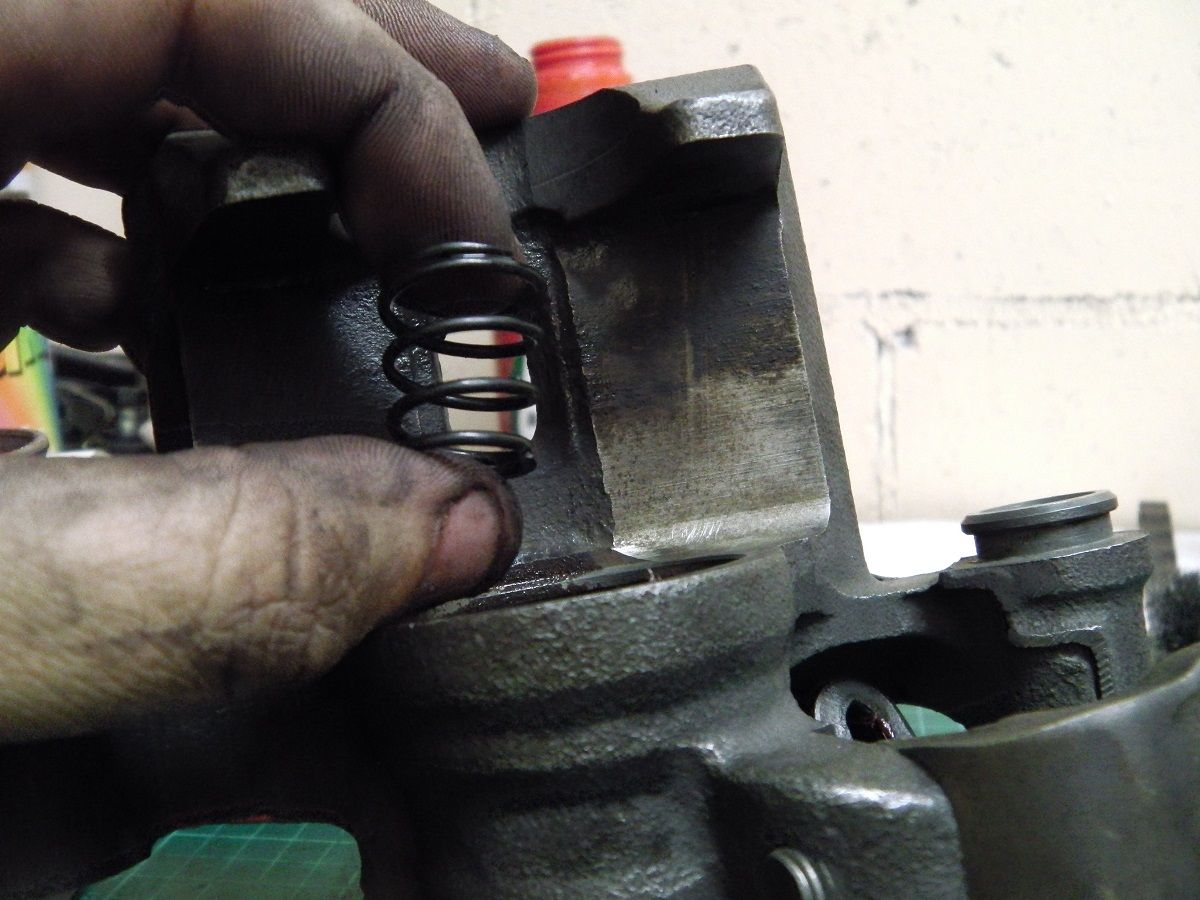
The easiest way to do this is to drop them down on to the spindle and then using the circlip plier head/needle nose pliers combo, get the circlip down as far as you can. You won't be able to get the circlip on like this as the spring is pushing it back up.
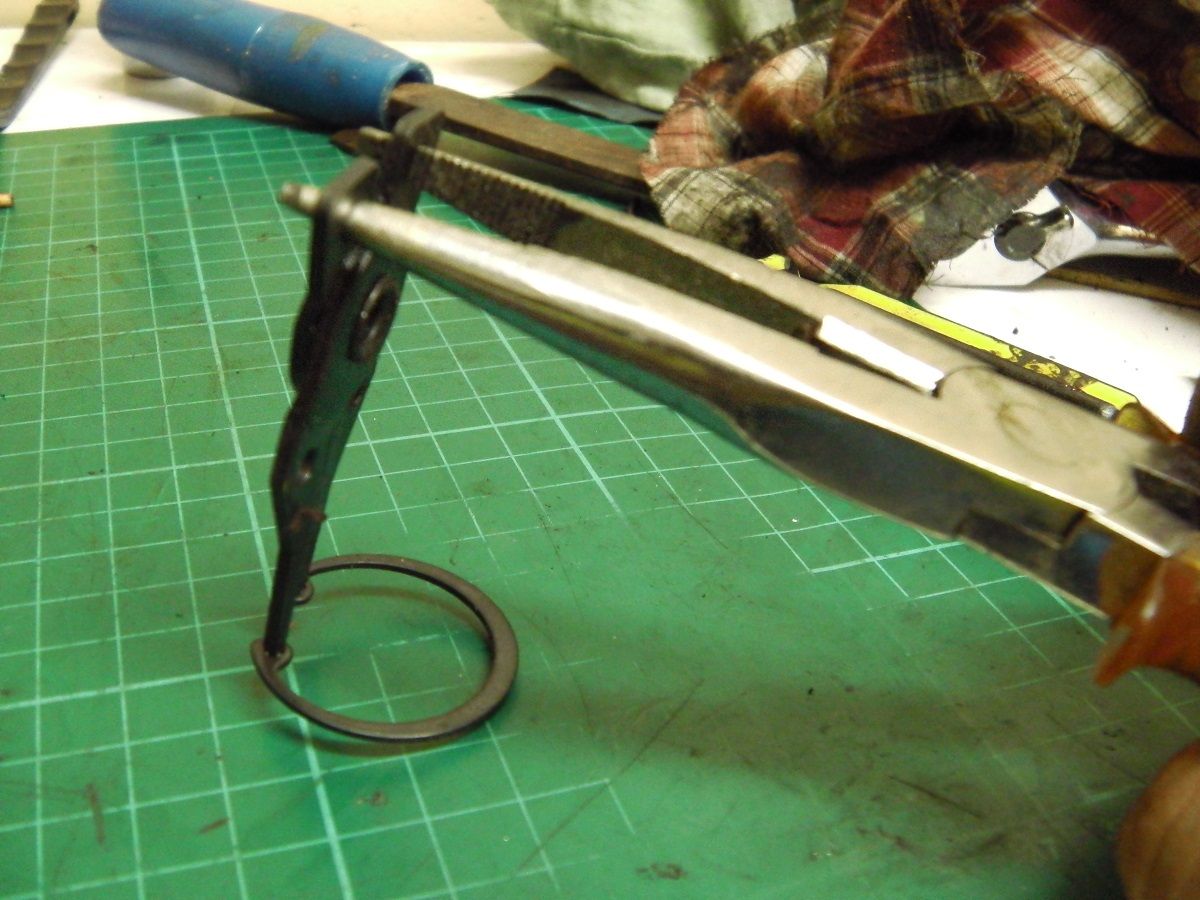
What you need to do is find a socket that is just a tiny bit smaller than the bore and using some force press down on the circlip until the spring compresses enough allowing the circlip to seat.
Step 18: Coat the piston with brake fluid and stretch the new dust boot over it.
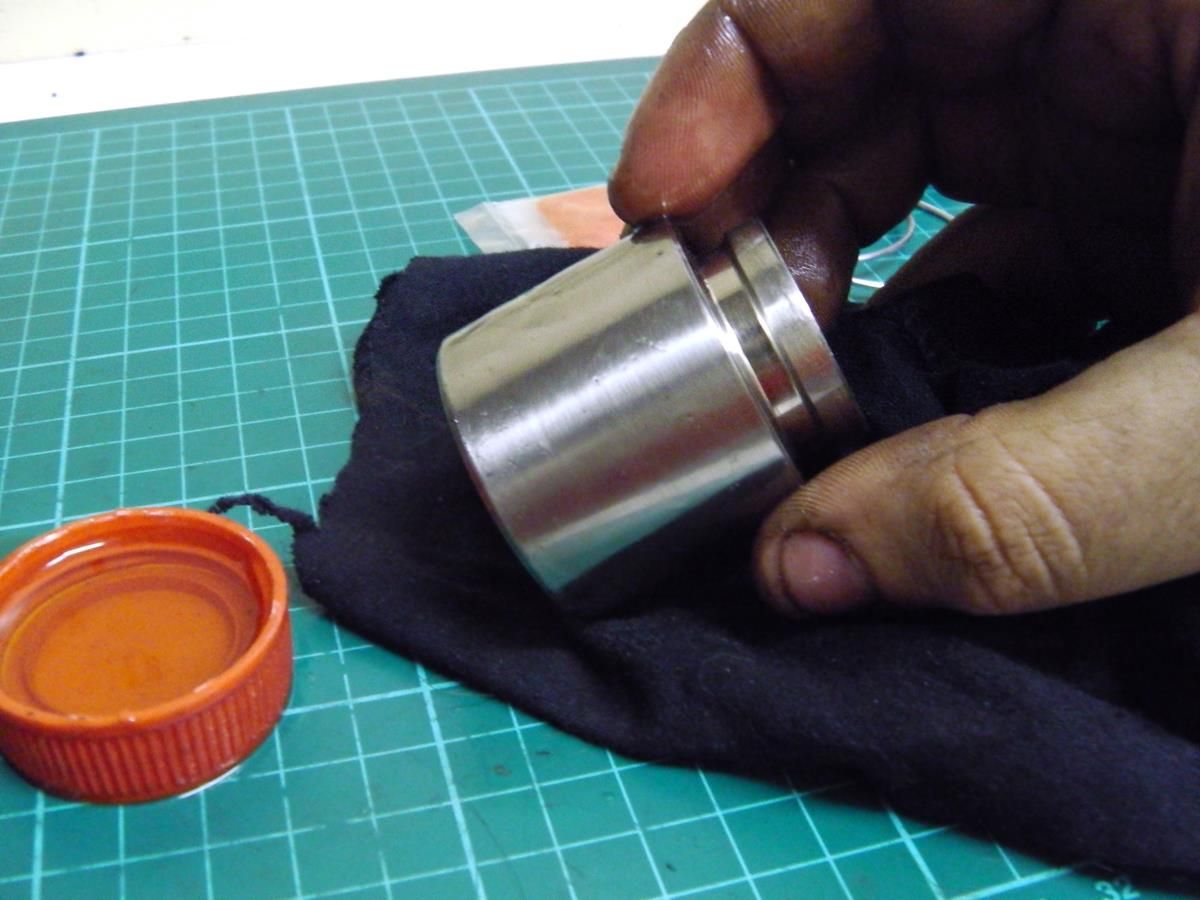
Step 19: Screw the piston back into the caliper.
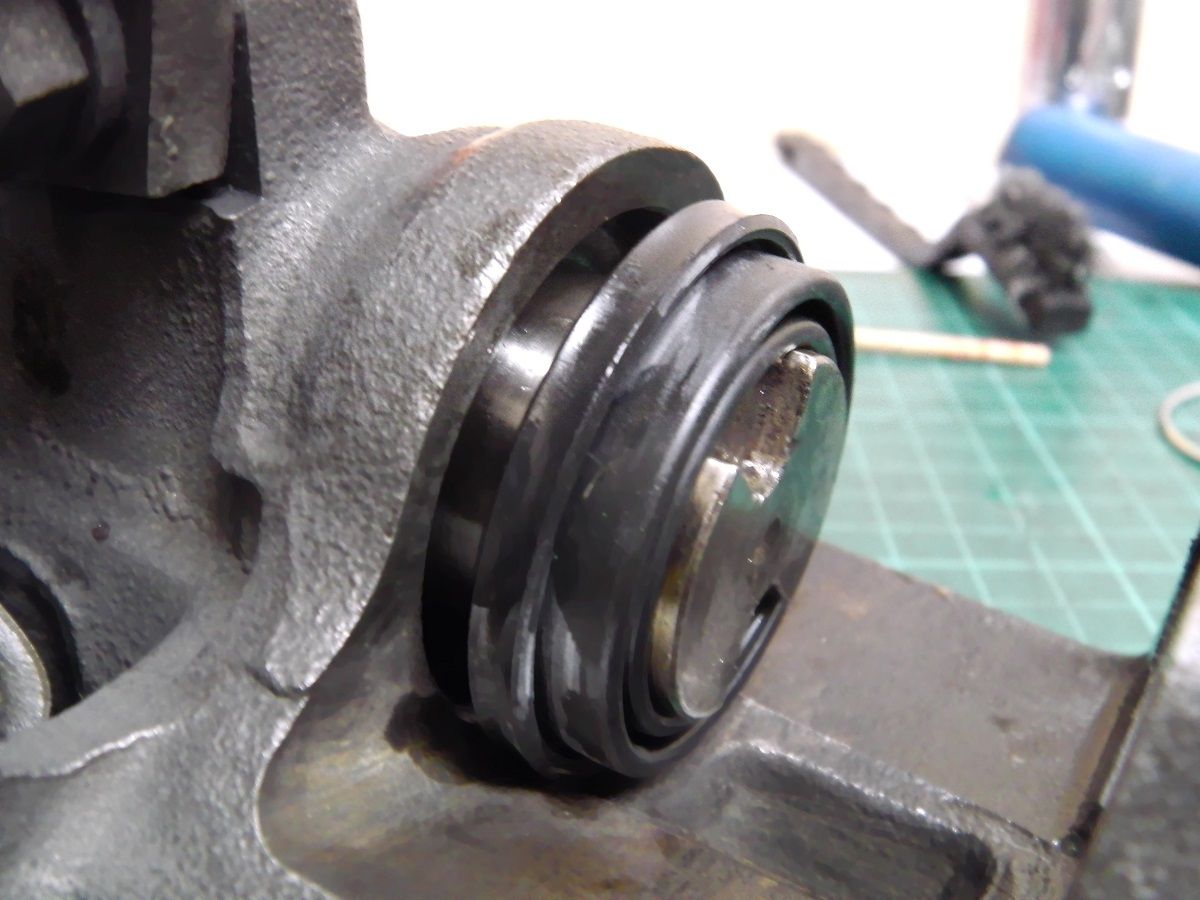
Step 20: Using a skewer or dull flat head screwdriver, push the edge of the dust boot into the groove on the caliper.
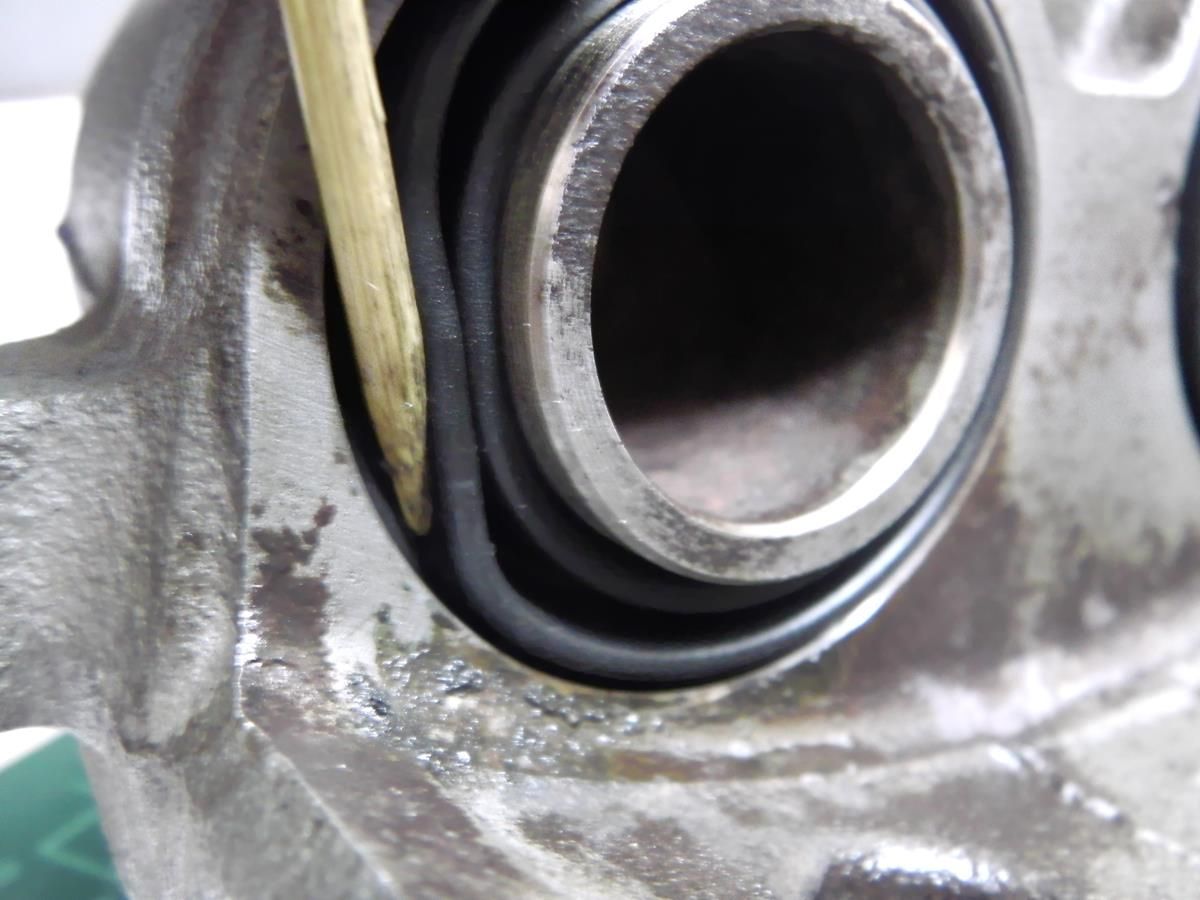
The dust boot has a lip that sits flush with the groove and you need to make sure it is all the way in. I took a photo showing what it looks like when it isn't seated properly.
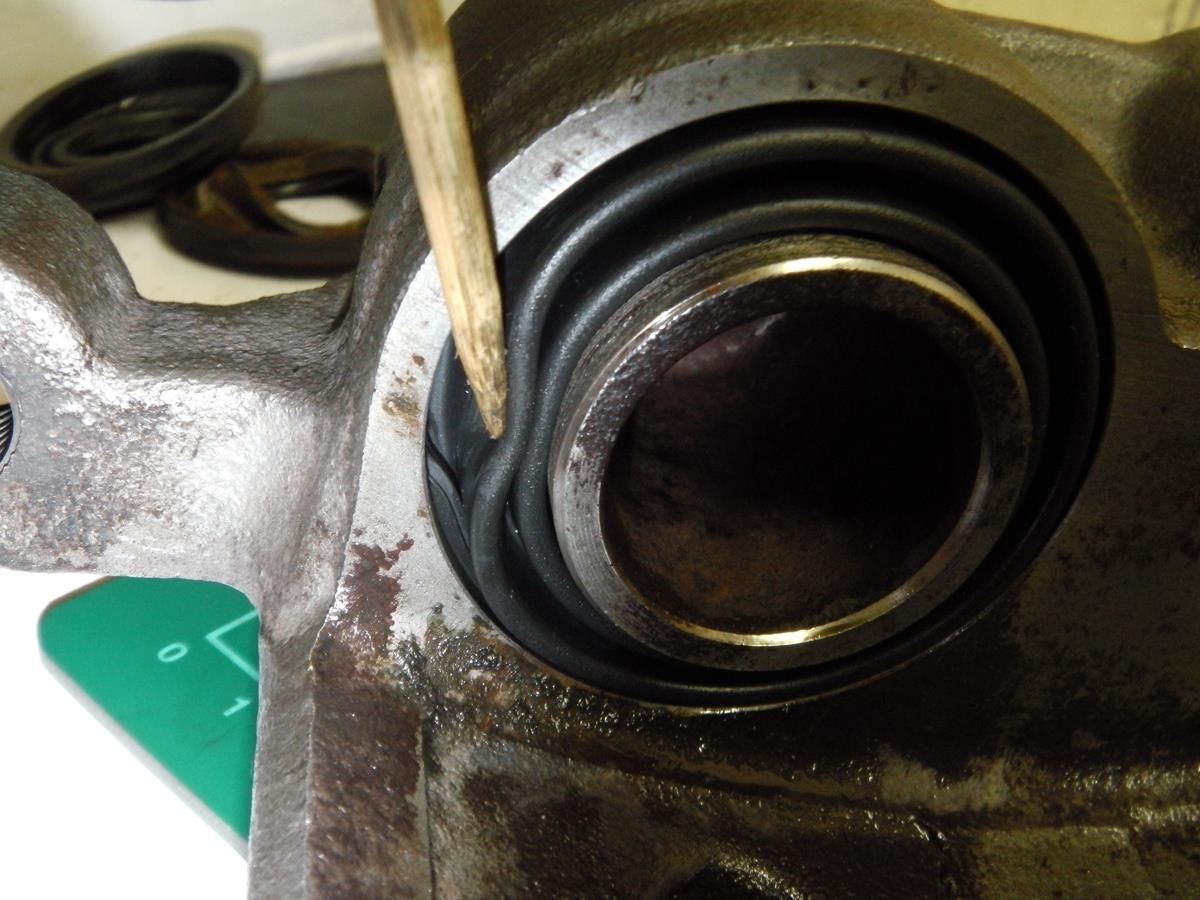
Step 21: Insert the new retaining ring, this may be a little tricky but I found the best way is to insert one side and then kind of twist and push it.
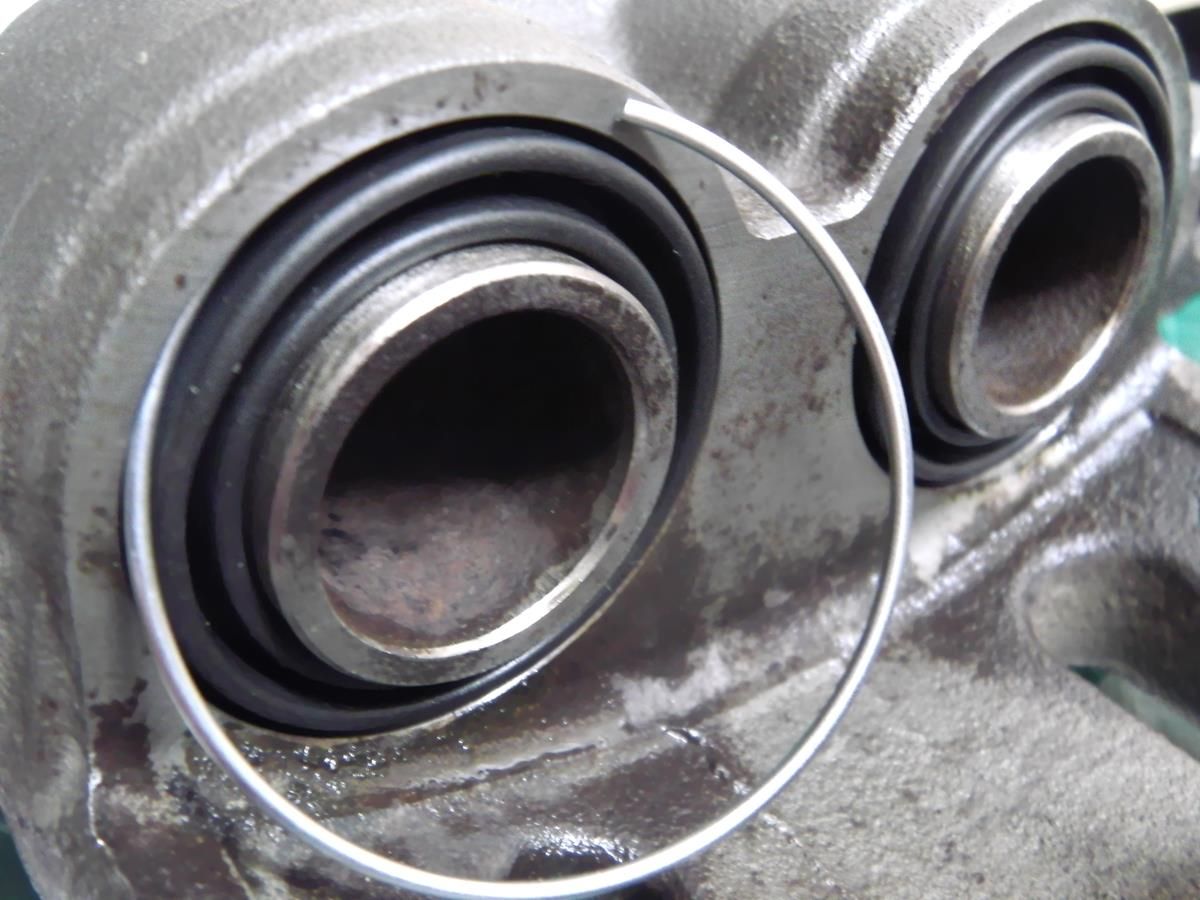
Step 22: We need to twist the piston back out again to make sure the dust boots are seated properly. Once you have done this, twist it back in.
The remaining boots in the kit are for the slide pins. One of them has a metal sleeve through it. Remove the sleeve first before trying to remove the boot. Install the new boots and then grease the sleeve and push it in.
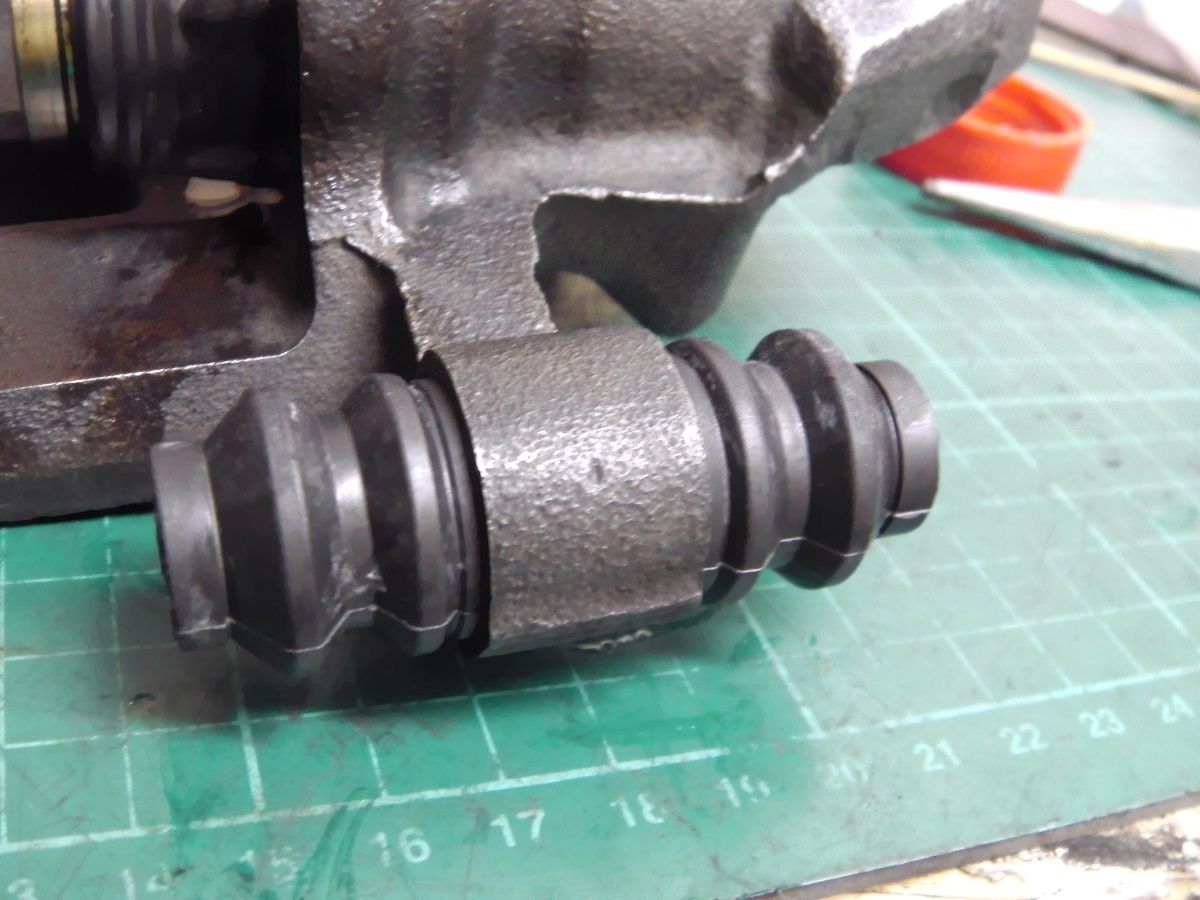
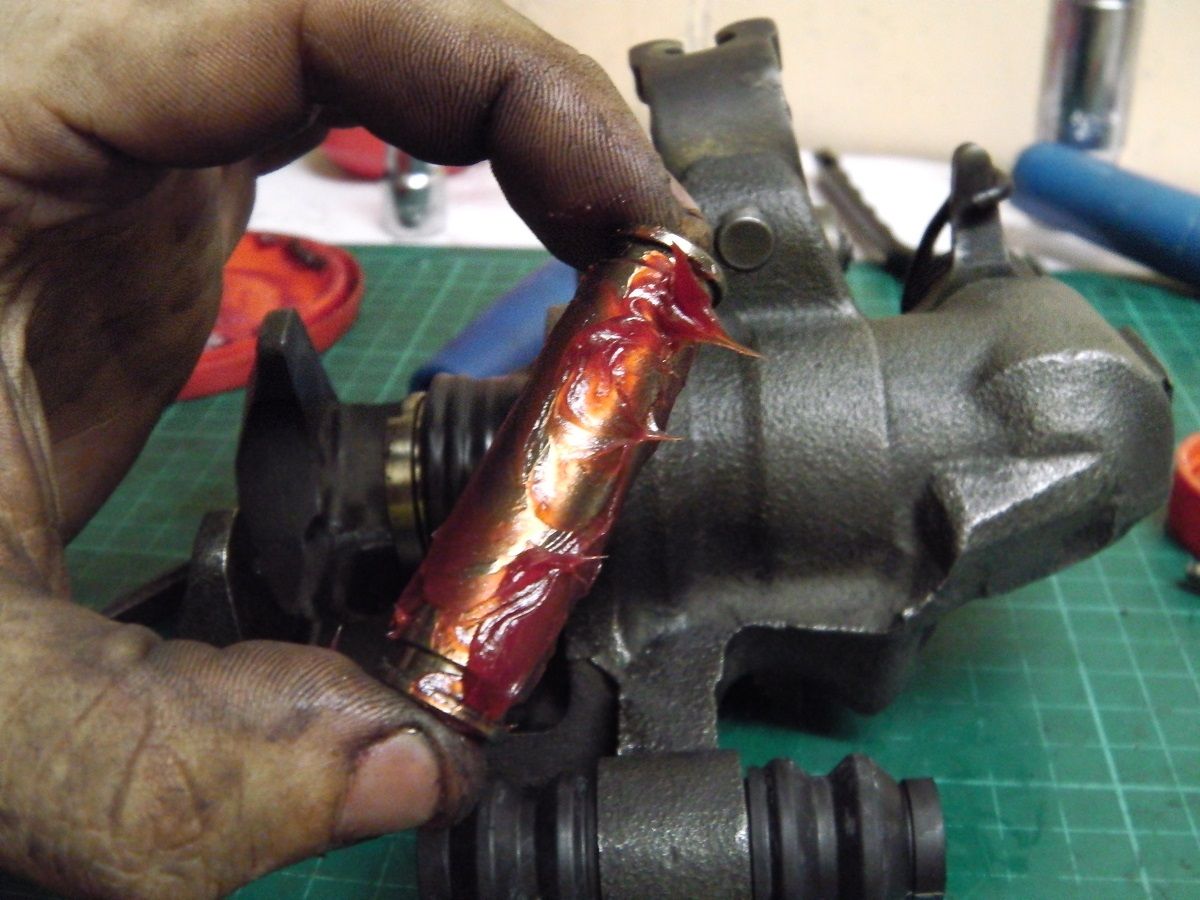